Abschnitt 5.3 - 5.3 Maschineller Vortrieb (Tunnelbohrmaschine (TBM))
5.3.1 Allgemeines
In den letzten Jahren werden Arbeiten in Druckluft zunehmend im maschinellen Tunnelvortrieb durchgeführt. Hierzu zählen:
Schildvortrieb mit flüssigkeitsgestützter Ortsbrust (Hydroschild)
Schildvortrieb mit Erddruckstützung (Erddruckschild)
Druckluftschild
Beim Einsatz von Hydroschilden oder Erddruckschilden finden Arbeiten in Druckluft nur über kurze Zeiträume (eine Schicht bis wenige Tage) statt. Dabei werden die in der Arbeitskammer Beschäftigten für die Dauer der Arbeiten (Kontrollarbeiten, Werkzeugwechsel, Hindernisbeseitigung, usw.) in Druckluft exponiert.
Beim Einsatz von Druckluftschilden finden Arbeiten in Druckluft über die gesamte Vortriebsdauer (mehrere Tage/ Wochen/Monate) statt. Dabei werden die im Druckluftschild Beschäftigten arbeitstäglich exponiert.
In den nachfolgenden Anforderungen und Maßnahmen werden auch solche beschrieben, die ausschließlich beim Einsatz von Hydroschilden Relevanz haben. |
---|
In Zusammenhang mit dem maschinellen Tunnelvortrieb sind auch Kap. → 5.1 und Kap. → 5.2 zu berücksichtigen.
5.3.2 Gerätetechnische Anforderungen
Die technischen Anforderungen und die technische Ausrüstung der TBM ergeben sich aus:
Druckluftverordnung, insbesondere Anhang 1
RAB 25, Arbeiten in Druckluft (Konkretisierungen zur Druckluftverordnung), Teil 3 und Anhang
DIN EN 12110 Tunnelbaumaschinen - Druckluftschleusen - Sicherheitstechnische Anforderungen
DIN EN 16191 Tunnelbaumaschinen - Sicherheitstechnische Anforderungen
DWA-A 125 Rohrvortrieb und verwandte Verfahren
Weitere technische Anforderungen:
Zur Minimierung von Drucklufteinstiegen sind verschleißarme Materialien und Einrichtungen zur Verschleißüberwachung der Abbauwerkzeuge vorzusehen.
Für die Arbeiten in der Abbaukammer sind leicht montier- und demontierbare Podeste vorzusehen. Abmessungen und Aufnahmepunkte der Podeste sollten möglichst vereinheitlicht werden.
Anschlagpunkte für die persönliche Schutzausrüstung gegen Absturz (z. B. Höhensicherungsgerät) vorsehen.
Um die in der Abbaukammer Beschäftigten vor Fehlbedienungen von beweglichen Maschinenteilen, wie z. B. Schneidrad, Steinbrecher, Tauchwandschieber, zu schützen, dürfen diese nur mit Steuereinrichtungen vor Ort bedient werden. Dazu werden die Bedienelemente im Hauptsteuerstand, z. B. über einen Schlüsselschalter, gegen ungewollte Betätigung gesichert.
Werkzeugwechsel:
Um das Betreten des Gefahrbereiches vor dem Schneidrad zu vermeiden, sind möglichst von hinten am Schneidrad auswechselbare Abbauwerkzeuge vorzusehen.
Im Überdruckbereich (Schleusen und Arbeitskammer) sind notwendige Einrichtungen zum Transport/ Montage/Demontage der Abbauwerkzeuge zu planen und vorzusehen. Dazu sind Anschlagpunkte zum Einhängen von Lastaufnahmemitteln (z. B. Kettenzüge) vorzusehen und Arbeitsmittel zur sicheren Handhabung von schweren Lasten einzusetzen.
5.3.3 Verfahrenstechnische Anforderungen
5.3.3.1
Anfahrt der Tunnelbohrmaschinen (TBM) aus der Startbaugrube (Anfahrbrille)
Statische Berechnung für Anfahrbrille/Lasteinleitungspunkte, dafür sind die Lastannahmen (Luftdruck, Wasserdruck und sonstige Lasten) mit dem Prüfstatiker abzustimmen
Ortsbruststabilität nachweisen (Statik, vorhandene Verkehrslasten berücksichtigen, Störungen z. B. durch tiefe Rohrgräben, Leitungen und im Boden belassener Baugrubenverbau beachten)
Wenn notwendig Bodenverbesserungsmaßnahmen vorab durchführen
Maßnahmen gegen ein mögliches Abkippen des Schildes bereits bei der Planung berücksichtigen
Abdichtung zwischen Anfahrbrille und Schildmantel überwachen
Abdichtung zwischen Anfahrbrille und Tübbing überwachen
Nachdichtmöglichkeit der Dichtungen vorsehen (z. B. Verpressschläuche, Injektionsöffnungen, Dichtmaterial vorhalten)
Während des Anfahrvorganges sollten Druckluftarbeiten möglichst vermieden werden
5.3.3.2
Anforderungen an die Ortsbruststabilität bei Druckluftarbeiten
Eigenschaften der Bentonitsuspension wie z. B. Dichte, Fließgrenze, Filtratwasserabgabe festlegen und überwachen.
Bei Bedarf Austausch der Suspension in der Abbaukammer gegen Frischbentonit mit den erforderlichen Eigenschaften vornehmen.
Die Stützdruckberechnung einschließlich des Nachweises der Ausbläsersicherheit ist für alle maßgeblichen Betriebszustände (Erdbrei- oder Flüssigkeitsstützung, sowie Luftstützung) vorzunehmen. Ist eine (Teil-) Luftstützung der Ortsbrust aus statischen Gründen nicht möglich, sind zusätzliche Maßnahmen wie z. B. eine Bodenverbesserung zu prüfen.
Vor und während der Druckluftarbeiten ist der Luftverbrauch zu dokumentieren und die Ortsbrust ständig zu beobachten.
Siehe auch Kap. → 5.1.3.1
5.3.3.3
Durchführung des Absenkvorgangs (Hydroschild)
Im Regelfall erfolgt die Absenkung der Stützflüssigkeit und Umstellung auf (Teil-) Druckluftstützung in der Abbaukammer, ohne dass sich Beschäftigte im Überdruckbereich aufhalten. Lediglich in Einzelfällen, z. B. Arbeiten im innerstädtischen Bereich unterhalb von kritischen Strukturen, bei der Gefahr von Verklebungen in der Abbaukammer, kann die Anwesenheit von Beschäftigten zur visuellen Kontrolle in der Arbeitskammer erforderlich sein. Hierzu ist vor Aufnahme der Arbeiten eine fallbezogene Gefährdungsbeurteilung zu erstellen, in der das Gefährdungspotential für die Beschäftigten in Überdruck sowie das Gefährdungspotential Dritter evaluiert wird und Maßnahmen zur Vermeidung/Minimierung festgelegt werden.
Für die Ermittlung der Ausschleusungszeit der exponierten Beschäftigten ist der höchste erreichte Arbeitsdruck während des Aufenthalts in Druckluft maßgebend. |
---|
Ablauf des Absenkvorganges im Regelfall ohne Beschäftigte in der Arbeitskammer:
Information des Sicherungspostens an der Oberfläche über den Beginn des Absenkvorgangs und damit verstärkte Kontrolle des übertägigen Bereiches auf Besonderheiten (Setzungen, Luftblasen, Bentonitaustritte usw.), ggf. Einschleusen des Druckluftpersonals in die Arbeitskammer.
Kontrolle der Kommunikationseinrichtungen zwischen Druckluftpersonal und Schleusenwärter sowie Schildfahrer
Das Absenken des Bentonitspiegels zwischen Druck- und Tauchwand erfolgt in der Regel unter gleichzeitiger Anpassung (Erhöhung) des Druckes der Druckluftregelanlage, so dass der Stützdruck an der Ortsbrust gewährleistet bleibt.
Nach Erreichen des Absenkzieles und der Beruhigung der Druckluftregelanlage Beobachtung des Bentonitniveaus zwischen Druck- und Tauchwand
Vorsichtiges Öffnen des Ausgleichsschiebers in der Schildfirste zur Vermeidung von Druckschwankungen und Anpassung (Abregelung) des Druckes auf den für das festgelegte Absenkziel notwendigen Stützdruck.
Kontrolle der Luftverluste bzw. des Suspensionsspiegels nach Ausgleich zwischen Arbeitskammer und Abbaukammer
Einschleusen des Druckluftpersonals
Inbetriebnahme der Steuereinrichtungen für bewegliche Maschinenteile, wie z. B. Schneidrad, Steinbrecher, Tauchwandschieber, zur ausschließlichen Bedienung aus der Arbeitskammer
Vor dem Öffnen der Tauchwandtür ist über die Kontrollstutzen in der Tauchwand die Höhe des Suspensionsspiegels vor der Tauchwand zu kontrollieren, um sicher zu stellen, dass der Flüssigkeitsausgleich in der gesamten Abbaukammer stattgefunden hat.
Die einströmende Luftmenge von der Druckluftregelanlage ist zu überwachen. Bei starken Luftverlusten ist die Abbaukammer wieder mit Bentonitsuspension aufzufüllen. Ein erneutes Absenken ist erst nach Durchführung von weiteren Maßnahmen, z. B. Wartezeit, frische Bentonitsuspension, ggf. mit erhöhter Dichte, möglich.
Siehe auch Absenkschema Hydroschild in Anlage → 8.6
5.3.3.4
Vorbereitung der Arbeiten in der Arbeitskammer/Abbaukammer
Vor Beginn der Arbeiten ist eine gesonderte Arbeitsanweisung und/oder ein Erlaubnisschein gem. → Anlage 8.1 zu erstellen.
Bevor die Tür zur Abbaukammer geöffnet wird, ist der Schieber in der Druckwand vorsichtig zu öffnen, und zu überprüfen, dass sich in der Abbaukammer Druckluft und nicht Suspension bzw. Erdbrei befindet und der Druckausgleich stattgefunden hat.
Vorsichtiges Lösen der Verschraubung zum Öffnen der Druckwandtür. Bei unerwarteten Druckdifferenzen zwischen Arbeitskammer und Abbaukammer kann sich die Tür schlagartig unkontrolliert öffnen. Um die Druckwandtür bei einer Evakuierung jederzeit wieder druckdicht verschließen zu können ist die Türdichtung vor dem Betreten der Abbaukammer gründlich zu säubern. Vor dem Betreten der Abbaukammer ist eine Sichtkontrolle der Ortsbrust auf Anomalien (Risse, Ausbrüche, Filterkuchen, Steine usw.) vorzunehmen.
Einhängen der Arbeitspodeste und Leitern für den sicheren Stand
Reinigung des Arbeitsbereiches (Schneidrad, Podeste, Leitern, Handläufe, usw.) durch Abspülen mit dem Wasserschlauch. Dabei darf der Filterkuchen an der Ortsbrust durch den Wasserstrahl nicht beschädigt werden.
Benutzung von PSA gegen Absturz (Höhensicherungsgerät) durch Beschäftigte in der Abbaukammer.
Alle Beschäftigten in der Arbeitskammer sind zum Tragen von Auffang-/Rettungsgurten verpflichtet und haben sich an den dafür vorgesehenen Anschlagpunkten, z. B. mit einem Höhensicherungsgerät gegen Absturz (persönliche Schutzausrüstung gegen Absturz) zu sichern. Die Kommunikation zwischen den Beschäftigten in der Abbau-/Arbeitskammer und dem Steuerstand und dem Schleusenwärter ist jederzeit sicher zu stellen (Telefon/ Funkgerät).
Um die Druckwandtür jederzeit sofort schließen zu können dürfen keinerlei Leitungen durch die Türöffnung gelegt werden. Die Verlängerung der Versorgungsleitungen in die Abbaukammer hat über die dafür vorgesehenen Anschlüsse zu erfolgen. Um sich vor herabfallendem Boden aus der Ortsbrust zu schützen ist eine Kontrolle/Inspektion grundsätzlich aus dem rückwärtigen Bereich des Schneidrades durchzuführen.
Der Luftverbrauch und die Ortsbrust sind fortlaufend zu beobachten.
Unter Beachtung des notwendigen Stützdrucks ist der Flüssigkeitsspiegel auf dem vorgesehenen Absenkniveau zu halten.
Trockenbentonit vorhalten, um Beschädigungen des Filterkuchens reparieren zu können (Dickbentonit).
Bei steigendem Luftverbrauch ist die Ortsbrust z. B. mit Dickbentonit, Folie ggf. auch mit Spritzbeton zu versiegeln.
Bei zu hohem Luftverbrauch sind die Druckluftarbeiten zu unterbrechen. Durch Wiederauffüllung der Abbaukammer ist die sichere Ortsbruststützung wiederherzustellen, z. B. Auffüllen mit Bentonitsuspension beim Hydroschild.
5.3.3.5
Werkzeugkontrolle/Werkzeugwechsel am Schneidrad
Die Aufenthalts- und Ausschleusungszeiten sind wegen der erheblichen Arbeitsschwere in Abstimmung mit dem ermächtigten ärztlichen Fachpersonal anzupassen. |
---|
Durchführung der Werkzeugkontrolle/Werkzeugwechsel nach gesonderter Arbeitsanweisung und/oder Erlaubnisschein, siehe → Anlage 8.1
Beim Hydroschild ist das Schneidrad, wenn statisch möglich, um einige Zentimeter zurückzuziehen, damit der Filterkuchen an der Ortsbrust beim Drehen des Schneidrades nicht verletzt wird
Der Werkzeugwechsel sollte im oberen Bereich des Schildquerschnittes erfolgen, damit der Arbeitsdruck so gering wie möglich gehalten werden kann (s. Abb. 8)
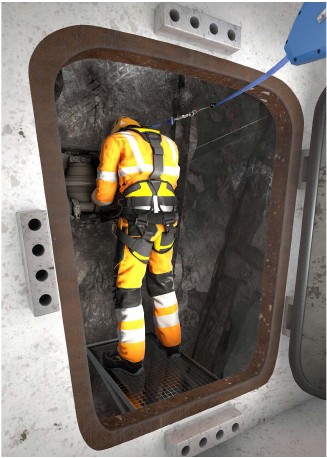
Abb. 8
Durchführen des Werkzeugwechsels im oberen Schildquerschnitt
Zur Demontage und Montage der Abbauwerkzeuge sind diese durch Verwendung der vorgesehenen Vorrichtungen gem. Kap. → 5.3.2 gegen Herunterfallen zu sichern
Wenn alle im oberen Bereich zugänglichen Abbauwerkzeuge gewechselt wurden, sind die Arbeitsbühnen zurückzubauen. Nun kann das Schneidrad mit den Steuereinrichtungen vor Ort weitergedreht werden. Nach erneuter Montage der Arbeitsbühnen wird der Werkzeugwechsel sukzessive fortgesetzt
5.3.3.6
Hindernisbeseitigung an der Ortsbrust
Die Aufenthalts- und Ausschleusungszeiten sind wegen der erheblichen Arbeitsschwere in Abstimmung mit dem ermächtigten ärztlichen Fachpersonal anzupassen. |
---|
Erstellen einer gesonderten Arbeitsanweisung und/ oder Erlaubnisschein gem. → Anlage 8.1
Zum Schutz der Beschäftigten vor herabfallenden Teilen (aus der Ortsbrust oder das Hindernis selbst), sind die Arbeiten möglichst aus dem rückwärtigen Bereich des Schneidrades auszuführen
Um bei der Beseitigung des Hindernisses einen sicheren Standplatz zu gewährleisten, kann der Einbau von zusätzlichen Arbeitsbühnen erforderlich sein
Vor dem Freilegen/Entfernen des Hindernisses ist dieses gegen unkontrolliertes Herabfallen (z. B. Kettenzug mit Ösenschraube, Hebebänder usw.) zu sichern
Das Freilegen des Hindernisses erfolgt durch Öffnung der Ortsbrust im unmittelbaren Umgebungsbereich. Der dazu geöffnete Bereich um das Hindernis ist schnellstmöglich wieder z. B. mit Dickbentonit, Spritzbeton, Holzverbau zu sichern.
Vorsichtiges Herauslösen der Hindernisse aus der Ortsbrust und zurückziehen in den rückwärtigen Schneidradbereich z. B. mit Kettenzug oder Winde
Erneutes Versiegeln der Ortsbrust in dem Bereich der Hindernisbeseitigung
Ggf. Zerkleinern des Hindernisses (z. B. Stemmhammer, Brennschnitt, Handsäge, hydraulisches Spaltgerät) in transportgerechte Stücke und Entfernen aus der Arbeitskammer
In Abhängigkeit von der Hindernisgröße und dem Umfang der Arbeiten zur Hindernisbeseitigung, kann die Freilegung in mehreren Abschnitten erforderlich werden und freigelegte Ortsbrust z. B. mit Spritzbetonsicherung gesichert werden.
5.3.3.7
Arbeiten bei Vollabsenkung
Eine Vollabsenkung ist nur bei Arbeiten im Sohlbereich der Maschine, wie z. B. am Steinbrecher oder der Förderschnecke, erforderlich. Die Bedienung der beweglichen Maschinenteile z. B. für Steinbrecher und Tauchwandschieber, erfolgt ausschließlich mit den Steuereinrichtungen in der Arbeitskammer.
Beim Einsatz von Hydroschilden ist der Tauchwandschieber nach Erfordernis zu schließen
Beim Einsatz von Erddruckschilden ist der Schneckenschieber an der Druckwand nach Erfordernis zu schließen
Die Ortsbrust ist insbesondere im oberen Bereich regelmäßig zu kontrollieren
Es dürfen keine Arbeiten im Sohlbereich ausgeführt werden, wenn die Gefahr besteht, dass aus dem oberen Bereich der Ortsbrust z. B. Steine oder ganze Blöcke unkontrolliert herabfallen können
Zu jeder Zeit sind Rückzugsmöglichkeiten hinter die Tauchwand/Druckwand sicherzustellen und eine Aufstiegsmöglichkeit hoch zur Personenschleuse freizuhalten
5.3.3.8
Schweißen, Schneiden und verwandte Verfahren in Druckluft
Die Aufenthalts- und Ausschleusungszeiten sind wegen der erheblichen Arbeitsschwere in Abstimmung mit dem ermächtigten ärztlichen Fachpersonal anzupassen. |
---|
In Kap. → 5.2.3.7 sind weitere Maßnahmen beschrieben.
5.3.3.9
Auffüllen der Abbaukammer (Hydroschild)
Nach Abschluss der Arbeiten in der Abbaukammer erfolgt ein Rückzug der Beschäftigten in den Bereich hinter der Tauchwand. Die Bentonitsuspension wird bis auf ein Niveau kurz unter der oberen Tauchwandtür, aufgefüllt.
Vor dem Schließen der Tauchwandtür ist deren Dichtung nochmals zu kontrollieren und ggf. zu reinigen.
Schließen des Ausgleichsschiebers in der Tauchwand
Rückzug der Beschäftigten in die Personenschleuse
Reinigen der Dichtungen der Personenschleusentür und Schließen der Schleusentür
Ausschleusen der Beschäftigten
Befüllen der Abbaukammer über die Speiseleitung und gleichzeitiges Öffnen der Firstentlüftung im atmosphärischen Bereich
Schließen der Firstentlüftung nach Bentonitaustritt im Schildschwanz
5.3.3.10
Ausfahrt der Tunnelbohrmaschine (TBM) in die Zielbaugrube (Ausfahrtopf)
Lastannahmen (Luftdruck, Wasserdruck und sonstige Lasten) für die statische Berechnung von Ausfahrtopf/ Deckel/Lasteinleitungspunkten sind mit dem Prüfstatiker bzw. der Prüfstatikerin abzustimmen
Max. Belastung aus Druckluft/Wasserdruck begrenzen (z. B. Überdruckventil)
Ausfahrtopf auf Dichtigkeit prüfen, Verfahren vorab festlegen
Ggf. Personenschleuse als zusätzlicher Zugang von der Zielbaugrube/vom Zielschacht aus vorsehen (s. Abb. 9)
Abnahme durch Prüfstatiker bzw. Prüfstatikerin
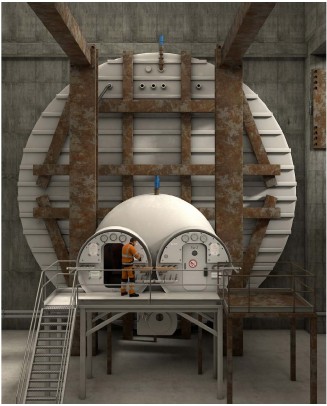
Abb. 9
Ausfahrtopf mit Personen- und Materialschleuse als zusätzlicher Zugang von der Zielbaugrube
5.3.3.11
Besonderheiten in Abhängigkeit vom Durchmesser der Tunnelbohrmaschine (TBM)
Besonderheiten bei kleinen Durchmessern:
Bei Rohrvortrieben mit möglichem Personaleinsatz unter Druckluft müssen die Schleusen eine lichte Höhe von mind. 1,60 m haben. Befinden sich ständige Arbeitsplätze in der Arbeitskammer müssen die Beschäftigten während der Arbeit aufrecht stehen und Geräte gefahrlos bedienen können. Im Arbeitsblatt DWA - A 125 ist eine lichte Höhe von mind. 1,80 m gefordert.
Bereits in der Planungsphase sollte der Einsatz eines größeren Durchmessers zugunsten der Sicherheit in der Vortriebsphase mittels einer Gefährdungsbeurteilung untersucht werden. Oftmals werden nur die Mindestanforderungen an den Rohrquerschnitt unter Vernachlässigung der Aspekte Arbeitssicherheit und Ergonomie erfüllt.