Abschnitt 3.3 - 3.3 Gefährdungen und Maßnahmen bei der Verwendung spezieller Arbeitsmittel im Spritzgießbetrieb
3.3.1
Bereitstellen von persönlichen Schutzausrüstungen
Nicht immer lassen sich Gefährdungen durch technische und organisatorische Maßnahmen vermeiden. Stellen Sie Ihren Beschäftigten geeignete persönliche Schutzausrüstungen zur Verfügung und setzen Sie deren Benutzung konsequent durch. Das alleinige Zurverfügungstellen persönlicher Schutzausrüstungen reicht als Schutz vor Gefährdungen nicht aus.

Abb. 58
Persönliche Schutzausrüstungen

Abb. 59
Alternative Persönliche Schutzausrüstungen je nach vorliegender Gefährdung
![]() | Rechtliche Grundlagen |
---|---|
|
![]() | Weitere Informationen |
---|---|
|
![]() | Gefährdungen |
---|
Viele Gefährdungen lassen sich durch technische und organisatorische Schutzmaßnahmen nicht restlos beseitigen. Um die Beschäftigten auch vor den Restrisiken zu schützen, müssen Sie diesen geeignete persönliche Schutzausrüstungen zur Verfügung stellen.
Das Tragen persönlicher Schutzausrüstungen bedeutet immer eine zusätzliche körperliche Belastung der Beschäftigten. Zudem ist das Tragen persönlicher Schutzausrüstungen trotz betrieblicher Vorgaben immer willensabhängig. Daher sind technische und organisatorische Schutzmaßnahmen vorrangig durchzuführen.
Mögliche Gefährdungen, bei denen persönliche Schutzausrüstungen zum Einsatz kommen kann, sind u. a.:
Gefährdung der Augen durch spritzende, heiße Kunststoffschmelzen an der Düse, an Heißkanälen etc.
Gefährdung der Augen durch herumfliegende Späne beim Entgraten oder Spritzer von Gefahrstoffen beim Reinigen etc.
Gefährdung der Füße durch Anstoßen, Herabfallen schwerer Gegenstände oder die Handhabung von Transportmitteln wie Handhubwagen oder Gabelstapler.
Gefährdung der Hände durch heiße Oberflächen bzw. Medien, z. B. Kunststoffschmelze oder an der Plastifiziereinheit, am Spritzgießwerkzeug, an den Temperiergeräten, Thermalölen, Heißkanälen.
Gefährdung der Hände durch Kontamination mit Gefahrstoffen beim Reinigen etc.
Gefährdung der Hände durch Messer, Schraubendreher, Beitel etc. und scharfkantige Oberflächen, z. B. an Auswerfern, Trennkanten, Formteilen.
Gefährdung der Unterarme durch heiße Oberflächen und Medien, z. B. Kunststoffschmelze oder an der Plastifiziereinheit, am Spritzgießwerkzeug, an den Temperiergeräten, Thermalölen, Heißkanälen.
Gefährdung des Kopfes durch Anstoßen, insbesondere beim Einbau von Spritzgießwerkzeugen.
Gefährdung des Gehörs durch Lärm.
![]() | Maßnahmen |
---|
Ermitteln Sie anhand der Gefährdungsbeurteilung, bei welchen Tätigkeiten welche persönlichen Schutzausrüstungen zu tragen sind. Schreiben Sie dies in Betriebsanweisungen fest, unterweisen Sie Ihre Beschäftigten diesbezüglich und setzen Sie das Tragen der festgelegten persönlichen Schutzausrüstungen konsequent durch. Das Tragen ist für alle Beschäftigten verpflichtend!
Folgende Tabelle gibt Ihnen einen Überblick, bei welchen Tätigkeiten Sie welche persönliche Schutzausrüstungen einsetzen können.
Tätigkeit | Persönliche Schutzausrüstung | |||||||||
---|---|---|---|---|---|---|---|---|---|---|
Sicherheitsschuhe | Schnittschutzhandschuhe | Hitzeschutzhandschuhe | Chemikalienschutzhandschuhe | Langärmlige, enganliegende Kleidung | Hitzefeste Unterarmlinge | Schutzbrille | Visier | Anstoßkappe | Gehörschutz * | |
Bedienen von Spritzgießmaschinen im Serienbetrieb | X | X | ||||||||
Einrichtbetrieb | X | X | X | X | X | X | ||||
Störungsbeseitigung | X | X | X | X | X | |||||
Produktwechsel und Reinigung | X | X | X | X | X | X | ||||
Reparatur und Instandhaltung | X | X | X | X | X | X | ||||
Innerbetrieblicher Transport und Verkehr | X | |||||||||
Entgratungsarbeiten | X | X | X | X | ||||||
Sortierarbeiten | X | X | ||||||||
Montagearbeiten | X | X | ||||||||
Granulataufgabe manuell | X | |||||||||
Zugabe von Einlegeteilen | X | X | ||||||||
Tätigkeit mit Gefahrstoffen | X | X | X | |||||||
Bedienen von Mühlen | X | X | X |
Beste Praxis
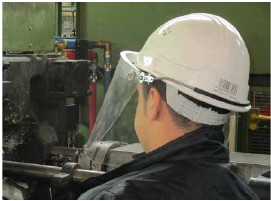
Abb. 60
Beschäftigter mit Gesichtsschutz beim Produktwechsel
3.3.2
Verwenden von Leitern und Tritten
Der Einsatz von tragbaren Leitern und Tritten birgt in der betrieblichen Praxis ein hohes Gefährdungspotential. Bereits der Sturz aus geringen Höhen kann schwerste Verletzungen zur Folge haben. Daher ist die Verwendung von Leitern nur unter bestimmten Voraussetzungen zulässig. Setzen Sie nach Möglichkeit feste Aufstiege wie Treppen, Podeste oder Hubarbeitsbühnen ein.
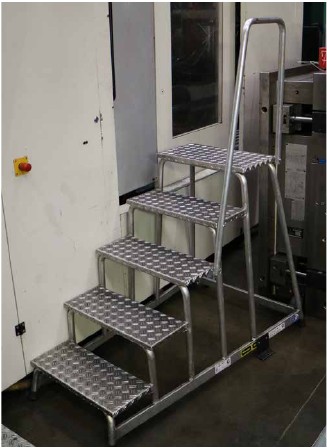
Abb. 61
Aufstiegshilfe
![]() | Rechtliche Grundlagen |
---|---|
|
![]() | Weitere Informationen |
---|---|
|
![]() | Gefährdungen |
---|
Die Verwendung von Leitern als hochgelegener Arbeitsplatz ist bis zu einer Standhöhe von 2 m und bei zeitweiligen Arbeiten bis zu einer Standhöhe zwischen 2 m und 5 m zulässig, wenn
aufgrund einer geringen Gefährdung und einer geringen Verwendungsdauer die Verwendung anderer, sichererer Arbeitsmittel nicht verhältnismäßig ist,
die Gefährdungsbeurteilung ergibt, dass die Arbeiten sicher durchgeführt werden können und
die Beschäftigten bei den Arbeiten mit beiden Füßen auf einer Stufe oder Plattform stehen können.
Bei Arbeiten auf Leitern und Tritten können beispielhaft folgende Gefährdungen auftreten:
Beim Besteigen von Leitern und Tritten besteht Absturzgefahr.
Auch der Absturz aus geringen Höhen kann schon zu schweren Verletzungen führen.
Bei beengten Platzverhältnissen und unebenen Böden besteht die Gefahr, dass Leitern nicht standsicher aufgestellt werden können.
Bei verschmutzten Leitern und Tritten besteht erhöhte Abrutschgefahr.
Witterungseinflüsse, insbesondere Wind, können die Standsicherheit der Leiter beeinflussen.
Leitern in Verkehrswegen stellen eine erhöhte Gefährdung für die Benutzenden der Leiter als auch für die Verkehrsteilnehmenden dar.
Beim Einsatz von Handwerkzeugen auf den Leitern besteht ebenfalls erhöhte Gefährdung.
![]() | Maßnahmen |
---|
Prüfen Sie eingehend vor Nutzung einer Leiter, ob diese zwingend erforderlich ist. Überlegen Sie, ob die Arbeiten nicht mit einem Hubsteiger o. ä. ausgeführt werden können. Wenn eine Leiter bzw. ein Aufstieg an einer Stelle regelmäßig erforderlich ist, sehen Sie fest installierte Aufstiege vor.
Beim Einsatz von Leitern und Tritten sind folgende Maßnahmen zu beachten:
Vor jedem Arbeitseinsatz muss durch die Nutzerin oder den Nutzer eine augenscheinliche Kontrolle auf offensichtliche Mängel durchgeführt werden (Sicht- und Funktionskontrolle).
Leitern und Tritte mit Schäden, die ihre sichere Verwendung beeinträchtigen, dürfen nicht weiterverwendet werden. Falls eine fachkundige Reparatur nicht möglich ist, empfiehlt es sich, die Leitern oder Tritte unverzüglich zu entsorgen. Dabei hat sich bewährt, diese zu zerkleinern, damit eine weitere Nutzung sicher ausgeschlossen wird.
Standsicherheit muss immer gewährleistet sein, z. B. durch an den Untergrund angepasste Leiterfüße, eine Fußverbreiterung, oder eine Holmverlängerung beim Einsatz auf Treppen.
Auf den richtigen Anstellwinkel bei Anlegeleitern muss geachtet werden.
Beim Arbeiten auf einer Leiter muss der Schwerpunkt immer zwischen den Leiterholmen liegen. Daher dürfen sich die Beschäftigten nicht hinauslehnen.
Setzen Sie möglichst für die jeweilige Leiter geeignetes Zubehör ein.
Sichern Sie den Arbeitsbereich, wenn dieser Bereich in Verkehrs- und Fahrwegen oder hinter Türen liegt.
Das Gewicht des mitzuführenden Handwerkzeuges und des Materials darf 10 kg nicht überschreiten.
Sehen Sie eine Ablagemöglichkeit für das Werkzeug an der Leiter vor.
Beschaffen Sie Werkzeugtaschen und -gürtel, damit sich die Beschäftigten beim Auf- und Abstieg sicher festhalten können.
Die Windangriffsfläche von mitgeführten Gegenständen darf nicht mehr als 1 m2 betragen.
Leitern und Tritte müssen in regelmäßigen Abständen von einer zur Prüfung befähigten Person geprüft werden.
An Leitern und Tritten müssen grundlegende Informationen als gut sichtbares Piktogramm zur Kennzeichnung angebracht sein. Diese beinhalten z. B. die maximale Belastung, Benutzerhinweise, sowie ggf. auch Angaben zur Prüfung.
Unterweisen Sie Ihre Beschäftigten vor der Benutzung von Leitern und Tritten sowie in regelmäßigen Abständen anhand der Gefährdungsbeurteilung und der Betriebsanweisung. Unterweisungen sind zu dokumentieren.
Für Anlegeleitern, Stehleitern, Merkzweckleitern und Tritte ergeben sich weitere individuelle Gefährdungen, die Sie u. a. der kurz und bündig-Schrift KB 009 "Leitern und Tritte" der BG RCI entnehmen können.
Beste Praxis
Viele Arbeiten, die auf Leitern ausgeübt werden, können auch auf einer Hubarbeitsbühne durchgeführt werden. Hubarbeitsbühnen bieten einen sicheren Stand und sind in vielen Bereichen einsetzbar. Weitere Informationen können Sie der DGUV Information 208-019 "Sicherer Umgang mit fahrbaren Hubarbeitsbühnen" entnehmen.
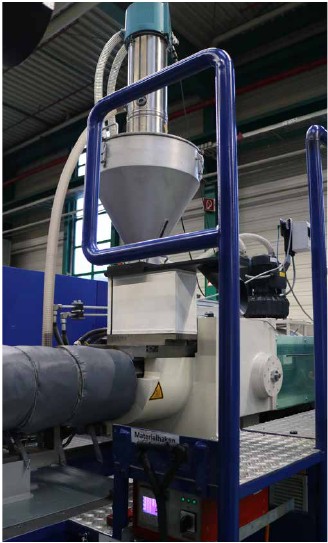
Abb. 62
Fest installierter Aufstieg an einer Spritzgießmaschine
3.3.3
Betreiben von Kranen
Eine ganze Reihe von Arbeitsaufgaben werden unter Einsatz von Kranen durchgeführt, wie Rüstarbeiten, Transport von Spritzgießwerkzeugen oder das Verstellen von Maschinen. Bei falsch angeschlagenen Lasten oder überlasteten Kranen besteht die Gefahr, dass die Lasten abstürzen können. Die Folge sind häufig sehr schwere oder tödliche Verletzungen.
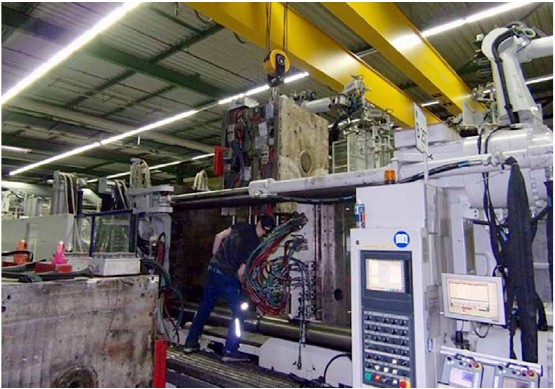
Abb. 63
Krananlage in einer Spritzgießfertigung
![]() | Rechtliche Grundlagen |
---|---|
|
![]() | Weitere Informationen |
---|---|
|
![]() | Gefährdungen |
---|
Beim Einsatz von Kranen können unter anderem folgende Gefährdungen auftreten:
Durch falsches Anschlagen der Lasten kann es zum Absturz der Lasten kommen. Dabei besteht die Gefahr, dass Personen von den herabfallenden Lasten erschlagen werden können.
Defekte Anschlagmittel oder deren Überlastung können beim Versagen ebenfalls zum Absturz der Lasten führen.
Durch zu schwere Lasten kann es zum Versagen einzelner Bauteile des Krans kommen. Dieses kann wiederum zum Absturz von Lasten führen.
Beim Einbau der Spritzgießwerkzeuge in die Maschinen kann es durch Pendelbewegungen zu schweren Quetschungen kommen.
![]() | Maßnahmen |
---|
Beim Einsatz von Kranen müssen Sie unter anderem auf folgende Punkte achten:
Wählen Sie den Kran und die Lastaufnahmeeinrichtungen nach den betrieblichen Gegebenheiten aus wie Traglast und/oder Transportaufgaben.
Es müssen erkennbar die Angaben über die höchstzulässigen Belastungen (Tragfähigkeit) am Kran und der Lastaufnahmeeinrichtung angebracht sein.
Erleichtern Sie die Bedienung, indem Sie den Kran mit zusätzlichen Symbolen versehen, die z. B. auf genaue Positionen hinweisen.
Sicherheitsabstände müssen eingehalten werden. Das gilt sowohl bei der Erstinbetriebnahme als auch bei Veränderungen im Arbeitsbereich. Bewegte Teile des Krans müssen mindestens 0,5 m Abstand zu Teilen der Umgebung haben.
Sorgen Sie für die Auswahl und Qualifizierung von geeignetem Personal für das Führen von Kranen und das Anschlagen von Lasten.
Stellen Sie sicher, dass eine unbefugte Kranbedienung verhindert ist.
Sorgen Sie für die Planung, Organisation und Durchführung von Prüfungen von Kran und Lastenaufnahmeeinrichtungen durch Prüfsachverständige (vor Inbetriebnahme, nach wesentlichen Änderungen, wiederkehrend), Sicht- und Funktionsprüfungen vor Arbeitsaufnahme durch den Kranführer bzw. die Kranführerin sowie für eine entsprechende Dokumentation (Prüfbuch).
Treffen Sie Regelungen, damit Wartung und Instandhaltungsarbeiten sicher erfolgen können (Abschalten, gefährdete Bereiche gegen Zutritt sichern, Kran gegen Wiedereinschalten sichern, kontrollierte Wiederinbetriebnahme/Freigabe nach den Arbeiten).
Kontrollieren Sie, dass sich der Kranführer oder die Kranführerin an die Vorgaben der Betriebsanweisung hält, z. B. ungehinderte Sicht auf die Last sicherstellen, Pendelbewegungen vermeiden.
Weisen Sie an, dass sich keine Personen unter schwebenden Lasten aufhalten und Abstand zum Gefahrenbereich gehalten wird.
Beste Praxis
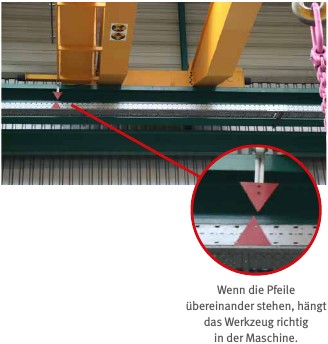
Abb. 64 a + b
Best Practice zur optimalen Positionierung der Kranbahn über der Maschine: Der Kran ist richtig positioniert, wenn die Pfeile übereinander stehen.
3.3.4
Betreiben von Förderbändern
Förderbänder werden oft in die Fertigungsabläufe integriert, um beispielsweise fertige Formteile oder Angüsse zu transportieren. Dadurch wird zum einen die Unfallgefahr im Bereich des innerbetrieblichen Verkehrs reduziert. Andererseits können sich durch Förderbänder neue Gefahrstellen, wie Quetsch-, Fang- und Einzugsstellen ergeben.
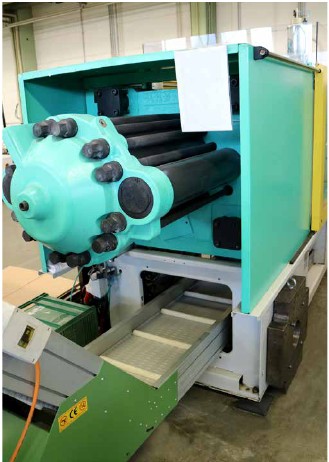
Abb. 65
Spritzgießmaschine mit Förderband
![]() | Weitere Informationen |
---|---|
|
![]() | Gefährdungen |
---|
Fertige Formteile, Angüsse und dergleichen werden oftmals mit Förderbändern transportiert. Die Formteile werden dazu beispielsweise mit einem Handlinggerät oder einem Industrieroboter aus der Maschine entnommen und auf einem Förderband abgelegt. In anderen Fällen fallen die Formteile aus der Maschine nach unten auf ein Förderband und werden von dort weitergefördert.
Auch diese Art der Automatisierung hilft, den innerbetrieblichen Transport und damit verbundene Unfallgefahren zu verringern.
Ein weiterer positiver Aspekt beim Einsatz von Förderbändern ist die Entlastung der Beschäftigten, da viele manuelle und ggf. auch belastende Handhabungen entfallen. Von den Förderbändern selbst gehen jedoch auch Gefährdungen aus:
Im Bereich der Antriebs- und Umlenktrommeln besteht die Gefahr des Einzugs.
Sind mehrere Förderbänder hintereinander gereiht, so besteht an den Übergangsstellen die Gefahr des Einzugs.
Wird mit Handwerkzeugen an laufenden Förderbändern gearbeitet, so können diese eingezogen werden.
Durch das reflexartige Nachgreifen, wenn das Handwerkzeug aus der Hand gerissen oder ein anderer Gegenstand eingezogen wird, können die Hände oder Arme eingezogen werden.
Sind Förderbänder in Bodennähe montiert, so besteht die Gefahr, darüber zu stolpern.
Lange Haare und weite Kleidung können auch an kleinen Einzugsstellen eingezogen werden. Dadurch kann es zu schweren Verletzungen kommen.
Um Förderbänder betreiben zu können, müssen unter Umständen Verdeckungen an Maschinen entfernt werden, beispielsweise im Bereich der Ausfallöffnung. Werden die Förderbänder entfernt, sind ggf. Gefahrstellen erreichbar, wenn die Verdeckungen nicht wieder angebracht wurden.
![]() | Maßnahmen |
---|
Die herstellerseitig angebrachten festen Schutzeinrichtungen an den Ausfallöffnungen sollten möglichst nicht entfernt werden. Falls dies aufgrund der Montage von Förderbändern erforderlich ist, stellen Sie sicher, dass diese festen Schutzeinrichtungen nach Entfernung des Förderbandes vor Wiederinbetriebnahme der Maschine wieder installiert werden.
Auch bei installierten Förderbändern darf ein Eingriff in Gefahrstellen durch die Ausfallöffnung nicht möglich sein. Beachten Sie hierbei auch, dass sich im unteren Bereich des Werkzeugs Quetschstellen durch Wasseranschlüsse u. ä. ergeben können, die ebenfalls gegen Eingriff gesichert werden müssen.
Förderbänder müssen fest installiert, also nur mit Werkzeug zu entfernen sein, wenn nach deren Entfernung Gefahrstellen erreichbar sind.
Müssen Förderbänder umgebaut, repariert oder instandgesetzt werden, so sind diese immer auszuschalten und gegen unbeabsichtigtes Wiedereinschalten durch Dritte zu sichern, zum Beispiel mit einem LOTO-System.
Müssen bodennahe Förderbänder überstiegen werden, so müssen Sie ein sicheres Übersteigen gewährleisten. Dieses können sie durch Stege, Treppen etc. realisieren.
Stellen Sie sicher, dass alle Auflauf- und Einzugsstellen an Förderbändern, insbesondere im Bereich der Antriebs- und Umlenktrommeln, durch Füllstücke oder durch trennende Schutzeinrichtungen, wie zum Beispiel durch Tunnel oder Schutzgitter, geschützt sind.
Störungen dürfen ausschließlich durch speziell dafür unterwiesene Beschäftigte beseitigt werden.
Ordnen Sie enganliegende Kleidung an. Lange Haare sind durch ein Haarnetz zu sichern.
Beste Praxis
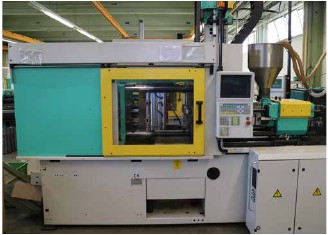
Abb. 66
Die Verdeckung an der Ausfallöffnung wurde nach dem Entfernen ordnungsgemäß wieder montiert, um den Eingriff in Gefahrstellen zu verhindern
3.3.5
Betreiben von Silos
Silos haben sich zur Lagerung von Kunststoffgranulaten bewährt, wenn große Mengen gleicher Kunststoffe eingesetzt werden. Siloanlagen bergen aber auch neue Gefahren, zum Beispiel beim Besteigen oder beim Einstieg (Befahren) in Silos. Auch die Einschränkung der Verkehrsflächen durch die Lkw-Stellflächen kann zu Gefährdungen und Unfällen führen.
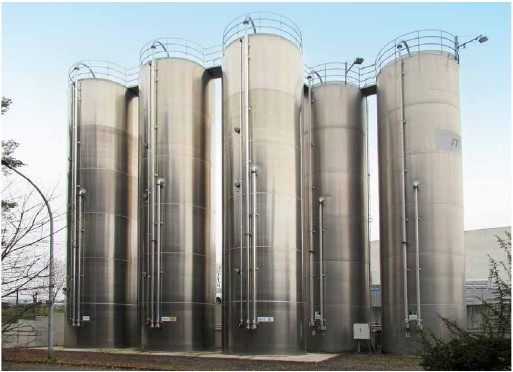
Abb. 67
Silos für Kunststoffgranulat
![]() | Rechtliche Grundlagen |
---|---|
|
![]() | Weitere Informationen |
---|---|
|
![]() | Gefährdungen |
---|
Silos haben sich zur Lagerung von Kunststoffgranulaten bewährt, wenn große Mengen gleicher Kunststoffe eingesetzt werden. Dies hat den Vorteil, dass die Granulate automatisch vom Silo zur Materialvorbereitung (z. B. Trocknung) oder direkt zur Maschine gefördert werden können. Gefährdungen können sich ergeben u. a. beim Besteigen, beim Einstieg sowie beim Befüllen der Silos.
Besteigen von Silos
Beim Besteigen von Silos ergeben sich insbesondere folgende Gefährdungen:
Absturz beim Besteigen der Siloanlagen, sowie beim Arbeiten auf den Silos.
Gefährdung bei der Rettung von Personen, die auf Silos tätig sind.
Einstieg in Silos
Auf den Einstieg in Silos sollte möglichst verzichtet werden, denn das "Befahren von Behältern" birgt eine Reihe von besonderen Gefährdungen.
Befüllen von Silos durch Silofahrzeuge
Bei der Befüllung der Silos durch Silofahrzeuge können sich folgende Gefährdungen ergeben:
Einengung der Verkehrswege durch die Silofahrzeuge.
Absturzgefahr, wenn Personen auf Silofahrzeuge steigen müssen.
Elektrostatische Aufladung bei der pneumatischen Förderung des Kunststoffgranulats.
Überfüllen des Silos bei fehlender Überfüllsicherung.
Das Platzen von Leitungen bzw. Schläuchen, wenn ein Überdruckventil fehlt und das Granulat mit Druck eingefüllt wird.
Zu gefährlichen Situationen kann es kommen, wenn das Silofahrzeug während des Befüllvorgangs losfährt.
Muss zur Restentleerung der Silobehälter am Fahrzeug gekippt werden, besteht die Gefahr des Umstürzens.
![]() | Maßnahmen |
---|
Besteigen von Silos
Prinzipiell sollte das Besteigen von Silos und das Einsteigen (Befahren) nach Möglichkeit vermieden werden. Ist dies unvermeidlich, so gilt:
Sorgen Sie dafür, dass an den Silos fest installierte Aufstiegshilfen wie Steigleitern mit Rückenschutz installiert sind.
Stellen Sie sicher, dass die Silos nur von Personen bestiegen werden, die dazu gesundheitlich in der Lage sind.
Bilden Sie Beschäftigte für die "Höhenrettung" aus, um ggf. verletzte Personen von den höher gelegenen Bereichen des Silos retten zu können. Oftmals haben auch ortsansässige Feuerwehren einen Höhenrettungstrupp.
Einstieg in Silos:
Sorgen Sie dafür, dass der Einstieg in Silos vermieden wird.
Beauftragen Sie einen Fachbetrieb mit dem "Befahren des Behälters", wenn dies erforderlich ist.
Detaillierte Informationen zum Thema "Einsteigen in Silos" enthalten die DGUV Regel 113-004 und die Internetseite
www.sicheres-befahren.de.
Befüllen der Silos durch Silofahrzeuge
Achten Sie darauf, dass die Silofahrzeuge eine ausreichend bemessene Stellfläche haben, die als solche auf dem Boden gekennzeichnet ist.
Diese Stellfläche sollte außerhalb viel befahrener innerbetrieblicher Verkehrswege liegen.
Sorgen Sie für einen ordnungsgemäßen Ausgleich zum Erdpotential durch Erdung der Schläuche nach Herstellervorgabe.
Sehen Sie an den Silos und deren Zuleitungen Überfüllsicherungen und Überdruckventile vor.
Stellen Sie sicher, dass das Silofahrzeug nicht während des Befüllvorganges losfahren kann. Dies kann durch Stopp-Schilder vor der Fahrerkabine, Unterlegkeile vor den Reifen o. ä. erfolgen.
Achten Sie auf eine ebene Standfläche für das Silofahrzeug und darauf, dass die Seitenstützen durch die Fahrerin oder den Fahrer des Siloahrzeugs ausgefahren werden.
Stellen Sie sicher, dass der Bereich um das Silofahrzeug nicht von Fußgängerinnen oder Fußgängern betreten wird, solange das Tranportsilo hochgefahren ist.
Beste Praxis
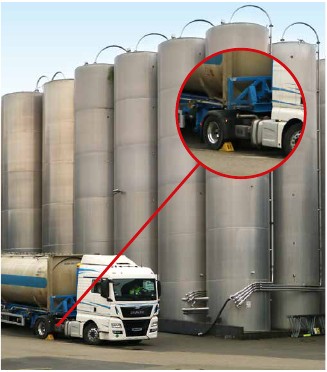
Abb. 68 a + b
Sicherung eines Silofahrzeuges gegen Wegrollen bei der Entladung durch Unterlegkeile
3.3.6
Materialversorgung
Die Versorgung der Spritzgießmaschinen mit Rohstoffen kann durch Entleerung von Säcken in den Trichter, durch das Befüllen von Zwischenbehältern oder automatisch durch pneumatische Förderanlagen erfolgen. Es ergeben sich beispielsweise Gefahren durch Lastenhandhabung, Rutschgefahren durch verunreinigte Böden und Schnittverletzungen beim Öffnen der Gebinde.
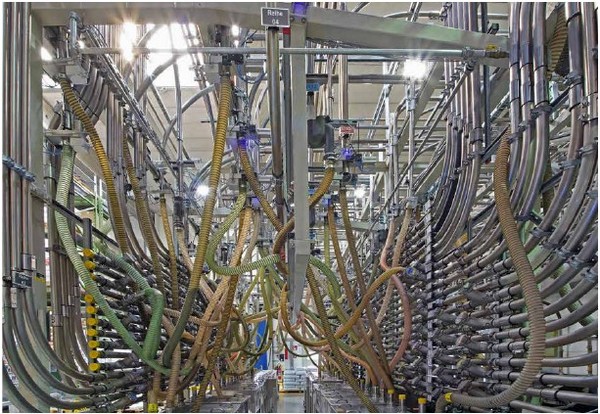
Abb. 69
Materialversorgung
![]() | Gefährdungen |
---|
Nur mit einer optimalen Materialversorgung ist eine reibungslose Produktion in Ihrem Spritzgießbetrieb möglich. Um diese komplexe logistische Aufgabe zu erfüllen, kommen je nach Maschinengröße und Produktionsmengen insbesondere folgende Möglichkeiten zur Anwendung:
Das Befüllen von Materialtrichtern und Zwischenbehältern (z. B. umfunktionierte "Mülltonnen") mit Granulat bzw. Masterbatch etc. aus Sackware.
Die pneumatische Saugförderung aus Zwischenbehältern, Trocknern, Oktabins, Big-Bags, Gitterboxen etc.
Die zentrale Materialversorgung mit pneumatischer Saugförderung aus Silos, Zwischenbehältern etc.
Bei diesen Tätigkeiten kann es beispielsweise zu folgenden Gefährdungen kommen:
Manuelles Entleeren von Sackware, Oktabins etc.
Bei kleineren Maschinen wird das Granulat, Masterbatch etc. meist aus den Säcken direkt in den Trichter gegeben. Auch Zwischenbehälter, Trockner, Fördereinrichtungen zur Befüllung von Silos etc. werden häufig manuell befüllt.
Beim Öffnen der Säcke, der Folieneinlagen in Oktabins etc. besteht die Gefahr von Schnittverletzungen durch Messer.
Durch verschüttetes Granulat, Masterbatch etc. besteht Rutschgefahr.
Ein hoch gelegener Materialtrichter kann zu Absturzgefahren führen.
Wenn in Förderschnecken eingegriffen werden kann, sind schwere Verletzungen möglich.
Das manuelle Heben und Entleeren von meist 25 kg schweren Granulatsäcken kann zu bandscheibenbedingten Schäden an der Wirbelsäule führen.
Es gibt Verbrennungsgefahren an der Plastifiziereinheit und an Trocknern.
Pneumatische Saugförderung
In vielen Fällen wird das Granulat, Masterbatch etc. durch pneumatische Saugförderung aus Silos, Zwischenbehältern, Trocknern, Oktabins, Big-Bags, Gitterboxen etc. zur Maschine gefördert.
Durch die Verwendung von Druckluft kommt es oftmals zu einer erheblichen Lärmbelastung.
Beim Kippen von Oktabins, Zwischenbehältern, Big-Bags, Gitterboxen etc. zur Restentleerung besteht die Gefahr, dass die Last umkippt und Ihre Beschäftigten verletzt.
Big-Bags, die nicht richtig gesichert sind, können aus der Aufnahme gleiten.
Beim Wechsel der Sauglanze oder der -anschlüsse besteht die Gefahr, dass Granulat ausläuft und zur Rutschgefahr wird.
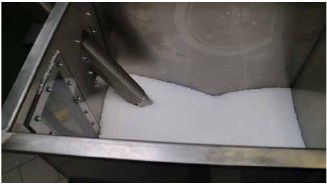
Abb. 70
Pneumatische Saugförderung
Zentrale Materialversorgung
Die Materialversorgung von zentraler Stelle ("Materialbahnhof", "Materialbühne") erfolgt mit pneumatischer Saugförderung aus Silos, Zwischenbehältern etc. Um die richtigen Förderwege zu garantieren, werden die Versorgungsschläuche meist umgesteckt.
Die bereits oben aufgeführten Gefährdungen gelten auch hier.
Beim "Umstecken" von Materialschläuchen müssen oft hochgelegene Bereiche erreicht werden. Dabei besteht ggf. Absturzgefahr.
Der Arbeitsbereich der zentralen Materialversorgung liegt meist abseits der Produktion und wird dann zum "Einzelarbeitsplatz".
![]() | Maßnahmen |
---|
Manuelles Entleeren von Sackware, Oktabins etc.
Testen Sie zusammen mit Ihren Beschäftigten, ob Sicherheitsmesser eingesetzt werden können. Dies ist beim Öffnen von Foliensäcken oftmals möglich. Stellen Sie Schnittschutzhandschuhe zur Verfügung und setzen Sie deren Nutzung konsequent durch.
Weisen Sie an, dass verschüttetes Granulat, Masterbatch etc. unverzüglich zu beseitigen ist.
Sorgen Sie dafür, dass der Materialtrichter mit einem festen Aufstieg leicht erreichbar ist.
Sichern Sie die Förderschnecke im unteren Bereich der Befüll- und Fördereinrichtungen gegen Eingriff durch den Einbau von Gittern (Sicherheitsabstände beachten).
Achten Sie auf eine ergonomische Gestaltung des Entleerbereichs mit guten Ablageflächen für die zu öffnenden Säcke.
Stellen Sie Hebehilfen, wie pneumatische Sackheber, zur Verfügung.
Bei Arbeiten am Trichter der Spritzgießmaschine sowie an Trocknern sind Schutzhandschuhe und Unterarmlinge zum Schutz gegen Verbrennungen zu tragen.
Pneumatische Saugförderung
Stellen Sie in Lärmbereichen Gehörschutz zur Verfügung und setzen Sie das Tragen durch.
Sichern Sie Oktabins, Zwischenbehälter, Big-Bags, Gitterboxen etc. beim Kippen zur Restentleerung vor dem Umstürzen, z. B. durch Spanngurte.
Big-Bags müssen sicher hängen, ohne aus der Halterung rutschen zu können.
Sorgen Sie dafür, dass verschüttetes Granulat unverzüglich aufgenommen wird.
Zentrale Materialversorgung
Die bereits vorstehend aufgeführten Maßnahmen gelten auch hier.
Verlegen Sie Bereiche, in denen Schläuche "umgesteckt" werden müssen, nach unten, damit sie ebenerdig erreichbar sind.
Beschaffen Sie für "Einzelarbeitsplätze" Notsignalanlagen.
Beste Praxis
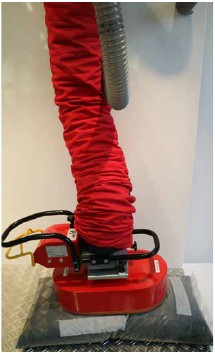
Abb. 71
Vakuumsackheber
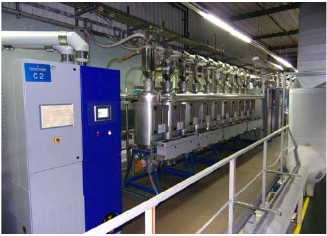
Abb. 72
Beispiel für eine zentrale Materialversorgung
3.3.7
Betreiben von Mühlen
In den meisten Spritzgießbetrieben werden Kunststoffe recycelt. Dazu werden beispielsweise Angüsse direkt an der Maschine eingemahlen und wieder zugeführt. In anderen Fällen werden Angüsse und Formteile sortenrein gesammelt und in Großmühlen zerkleinert. Es ergeben sich diverse Gefährdungen durch Lärm, Verunreinigungen, herausfliegende Reste etc.
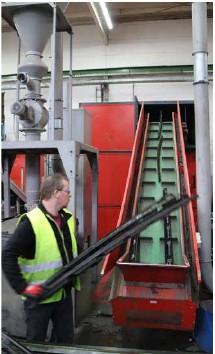
Abb. 73
Materialzufuhr zu Mühlen
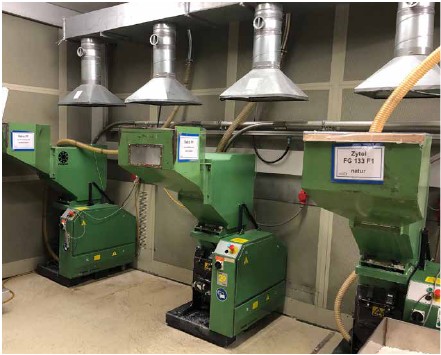
Abb. 74
Mühlen mit Absaugung
![]() | Gefährdungen |
---|
In Spritzgießbetrieben werden unterschiedliche Mühlen betrieben. Kleine "Anguss-Mühlen" neben einer Spritzgießmaschine zerkleinern Angüsse, kleine schadhafte Formteile etc., um sie wieder dem Produktionsprozess zuzuführen.
Serienbetriebe unterhalten oft eine eigene Abteilung, in der mit Großmühlen Angüsse und Fehlchargen eingemahlen werden, um sie der eigenen Fertigung wieder zuzuführen.
In Kunststoff-Mühlen wird das gesammelte Material über ein Förderband bzw. einen Einfüllschacht in die Mühle gegeben und dort mit Messern, die an einem Rotor montiert sind, zerkleinert.
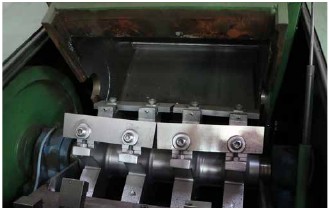
Abb. 75
Geöffnete Schneidkammer mit zugänglichen Messern auf der Rotorwelle im Inneren einer Mühle bei ausgeschalteter Maschine
Das Mahlgut wird per Schwerkraft oder durch pneumatische Förderung ausgetragen. Beim Recycling können folgende Gefährdungen auftreten:
Je nach Bauart der Mühle und den baulichen Gegebenheiten ist eine hohe Lärmbelastung in der Nähe der Mühle zu erwarten.
Aus der Einfüllöffnung können Materialreste herausgeschleudert werden, was insbesondere eine Gefahr für Augen und Hände darstellt.
Bei Messerwechseln besteht die Gefahr, sich an den scharfen Klingen zu schneiden. Dabei ist eine erhebliche Unfallgefahr gegeben, wenn der Rotor mit den Messern von Hand gedreht wird. Dies kann zufällig oder beabsichtigt sein, um zu testen, ob die Messer richtig sitzen.
Beim Messerein- und -ausbau kann es zu Verletzungen kommen durch Abrutschen mit Schraubenschlüsseln, Hämmern etc.
Bei Verstopfungen im Einfüllschacht besteht die Gefahr, sich zu verletzen, wenn in den Schacht hinein- bzw. nachgegriffen wird. Das gilt auch, wenn mit Stielen und dergleichen im Schacht manipuliert wird.
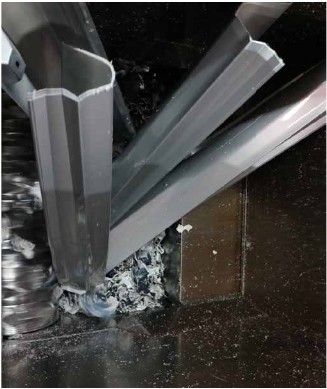
Abb. 76
Materialverstopfung
Durch ausgelaufenes Mahlgut besteht Rutschgefahr.
Bei höher gelegenen Einfüllschächten besteht Absturzgefahr. Ein Absturz kann auch schon bei geringen Höhen zu erheblichen Verletzungen führen.
Beim Hantieren mit großen Formteilen kann es zu ergonomischen Problemen durch ungünstige Körperhaltungen, schwere Lasten etc. kommen.
Beim Vorzerkleinern mit Band- oder Kreissägen sind Schnittverletzungen am Sägeblatt möglich.
Beim Besteigen von Förderbändern etc. besteht an Großmühlen die Gefahr, in die Mühle hineinzufallen.
In einigen Fällen findet eine Vorzerkleinerung in einem Schredder statt, nach der das Material mittels Förderschnecke in die Mühle gefördert wird. Wenn in die Förderschnecke eingegriffen wird, besteht die Gefahr von Amputationen.
![]() | Maßnahmen |
---|
Der Einfüllschacht muss so gestaltetet sein, dass niemand an die innenliegenden Werkzeuge gelangen kann.
Verwenden Sie möglichst "langsam laufende" Mühlen, da diese meist weniger Lärm emittieren. Dies hat sich insbesondere bei Angussmühle bewährt.
Stellen Sie in Lärmbereichen Gehörschutz zur Verfügung und setzen Sie die Benutzung durch.
Prüfen Sie die Nachrüstung mit Schallschutzhauben.
Lassen Sie die "Schutzvorhänge" (meist dicke Folie) am Einfüllschacht der Mühle regelmäßig erneuern.
Sorgen Sie dafür, dass bei Arbeiten an der Mühle Schutzbrille und Schutzhandschuhe, ggf. auch ein Visier, getragen werden.
Die Mühlenmesser sollten in speziellen Aufnahmen so gelagert werden, dass Schnittverletzungen durch unbeabsichtigtes Berühren vermieden werden.
Beim Umgang mit den Schneidmessern müssen Schnittschutzhandschuhe getragen werden.
Beim Messerein- und -ausbau muss die Mühle ausgeschaltet werden und gegen Wiedereinschalten gesichert werden (LOTO, s. Abschnitt 3.2.1.).
Sind verriegelt trennende Schutzeinrichtungen geöffnet, darf ein Starten nicht möglich sein.
Mühlen, die ab 2018 in Verkehr gebracht wurden, müssen über eine verriegelte trennende Schutzeinrichtung verfügen. Damit muss der Sicherheitsabstand zum Gefahrenbereich und unter Berücksichtigung der Öffnungszeit sichergestellt sein. Können bewegte Teile aufgrund ihrer Geschwindigkeit oder Beladung nachlaufen und ist die Öffnungszeit nicht wirksam, ist die Schutzfunktion um eine Zuhaltung zu erweitern. Diese Zuhaltung muss auch bei Energieausfall wirksam sein.
Der Rotor muss beim Ein- und Ausbau gegen unbeabsichtigtes Drehen gesichert werden. Die Antriebssysteme von Mühlen ab dem Baujahr 2018 müssen über eine konstruktive Lösung oder Blockiervorrichtung gegen unbeabsichtigtes Drehen verfügen. Ältere Maschinen müssen mit einer formschlüssigen Einlage am Rotor gesichert werden.
Stellen Sie sicher, dass nur intaktes Handwerkzeug verwendet wird. Veranlassen Sie arbeitstägliche Sichtprüfungen von Maulschlüsseln, Hämmern etc.
Stellen Sie sicher, dass auch beim Messerwechsel möglichst nur eine Person an der Mühle arbeitet.
Weisen Sie an, dass nicht in den Einfüllschacht gegriffen werden darf. Auch das Benutzen von Hilfsmitteln wie Stielen etc. ist zu untersagen, solange die Maschine in Betrieb ist.
Weisen Sie an, dass verschüttetes Mahlgut unverzüglich beseitigt wird.
Große Formteile sollten außerhalb des Mühlenbereiches mit Band- bzw. Kreissägen zerkleinert werden. Da dies mit weiteren Gefahren verbunden ist, nur besonders ausgebildetes Personal einsetzen.
Die Materialaufgabe sollte möglichst ebenerdig sein. Ist dies nicht möglich, sind fest installierte Podeste mit Zugangstreppen, ausreichenden Abstellmöglichkeiten für die Recyclingware etc. vorzusehen. Dabei darf die Höhe zur Unterkante der Aufgabeöffnung ab der Standfläche 1.200 mm nicht unterschreiten.
Sichern Sie ggf. die Absturzkante an der Paletten-Übergabestelle des Podestes gegen Absturz.
Untersagen Sie strikt, dass Förderbänder und dergleichen bestiegen werden. Dies gilt auch bei der Störungsbeseitigung, z. B. bei einem Materialstau.
Prüfen Sie die Verwendung von Transpondern, die von den Beschäftigten am Handgelenk, in der Warnweste oder im Sicherheitsschuh getragen werden und Förderband sowie Mühle stillsetzen, sobald sich die Person einem Gefahrbereich nähert.
Zur Störungsbeseitigung sind geeignete Aufstiegshilfen zu benutzen. Förderband und Mühle müssen sicher stillgesetzt sein.
Das Förderband muss mit einen Not-Halt (z. B. mit einer Reißleine als Betätiger für den Schalter) ausgerüstet sein.
Prüfen Sie zudem die Nachrüstung eines Not-Halts der Stoppkategorie 0 oder 1 für die Bedienplätze der Mühle.
Sichern Sie die Förderschnecke im Bereich der Befüll- und Fördereinrichtungen gegen Eingriff durch den Einbau von Gittern (Sicherheitsabstände beachten).
Beste Praxis
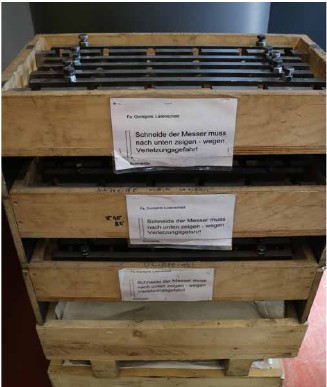
Abb. 77
Transportbehälter für Mühlenmesser zur Vermeidung von Schnittverletzungen
3.3.8
Betreiben von Industrierobotern, Handlingsystemen und Angusspickern
Zur Automatisierung der Produktion werden Industrieroboter, Handlingsysteme, Angusspicker und auch kollaborierende Robotersysteme eingesetzt. Die Bewegungsabläufe dieser Anbaugeräte sind oft sehr komplex und können von den Bedienenden nur schwer eingeschätzt werden. Dadurch kann es zu sehr schweren Unfällen kommen.
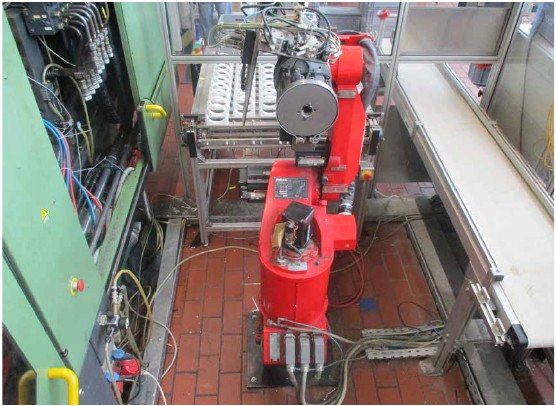
Abb. 78
Industrieroboter
![]() | Weitere Informationen |
---|---|
|
![]() | Gefährdungen |
---|
An Spritzgießmaschinen werden überwiegend zweiachsig arbeitende Anbaugeräte wie Handlinggeräte oder Angusspicker verwendet. Insbesondere bei größeren Spritzgießmaschinen kommen vermehrt Industrieroboter zum Einsatz. Auch kollaborierende Robotersysteme sind in der Praxis vorhanden. Es ist davon auszugehen, dass diese Systeme künftig zunehmend eingesetzt werden.
Von den Anbaugeräten können u. a. folgende Gefährdungen ausgehen:
Durch den Anbau der o. g. Peripheriegeräte ist es meist erforderlich, die Schutzeinrichtungen der Spritzgießmaschine zu verändern, damit das Gerät im Wirkbereich des Spritzgießwerkzeugs arbeiten kann. Damit ist es oftmals möglich, in den Gefahrbereich der Spritzgießmaschine zu gelangen.
Es ist beispielsweise beim Anbau eines Industrieroboters, Handlinggeräts bzw. Angusspickers an kleinen Spritzgießmaschinen erforderlich, die verriegelte Tunnelhaube von oben zu öffnen. Dadurch kann in das sich schließende Spritzgießwerkzeug eingegriffen werden.
Bei größeren Maschinen gilt sinngemäß dasselbe - meist ist der Eingriff in den Gefahrbereich von der Seite möglich, da z. B. die Schutztüre der Bediengegenseite für die Entnahme durch das Peripheriegerät geöffnet ist. Durch die teils sehr schnellen Bewegungen der Industrieroboter, Handlinggeräten, Angusspicker etc. kann es zu Quetsch-, Fang- und Scherstellen kommen. Ferner ist die Gefahr des Anstoßens oder Getroffenwerdens gegeben.
Die Bewegungen einer Industrieroboteranlage sind oft komplex und daher von den Bedienenden nur schlecht einzuschätzen.
Fehlerhaftes Verfahren der Industrieroboteranlage kann durch Steuerungsausfälle oder Bauteilversagen vorkommen. Dabei kann die produktionstechnisch festgelegte Schutzzone der Industrieroboteranlage verlassen werden.
Bei Fehlfunktion können Bau- oder Produktteile aus dem Produktionsraum geschleudert werden.
![]() | Maßnahmen |
---|
Die Arten des Einsatzes von Industrierobotern, Handlingsystemen, Angusspickern etc. sind vielfältig und komplex. Daher können hier nur allgemeine Grundsätze zur Sicherung solcher Systeme beispielhaft aufgezeigt werden. Die DGUV Information 209-074 "Industrieroboter" enthält weiterführende Vorgaben zu diesem Thema.
Grundsätzlich ist es erforderlich, die verkettete Anlage, bestehend aus Spritzgießmaschine und Peripheriegeräten wie Industrieroboter, Handlingsystem, Angusspicker etc. sicherheitstechnisch neu zu bewerten (siehe auch Abschnitt 3.2.7). Die sich neu ergebenden Gefährdungen lassen sich meist nicht von einer Anlage auf die nächste übertragen. Beurteilen Sie, welche neuen Gefahren sich durch den Anbau der Peripheriegeräte ergeben haben.
Sichern Sie die Gefahrbereiche der Spritzgießmaschine, die sich durch die Integration der Peripheriegeräte neu ergeben, gegen Zugriff bzw. gegen unbefugtes Betreten und stellen Sie sicher, dass das sicherheitstechnische Niveau der Spritzgießmaschine bei der Umsetzung der Maßnahmen nicht verringert wird.
Stellen Sie sicher, dass für die Gefahrbereiche, bei denen ein Ganzkörperzugang zu den Peripheriegeräten und der Maschine möglich ist, zusätzliche Schutzmaßnahmen ergriffen und zusätzliche Schutzeinrichtungen (z. B. Schaltmatten, Lichtvorhänge, Quittiersysteme, Einrichtungen gegen unbeabsichtigtes Schließen von verriegelten trennenden Schutzeinrichtungen, Lockout/Tagout-Systeme) bereitgestellt werden.
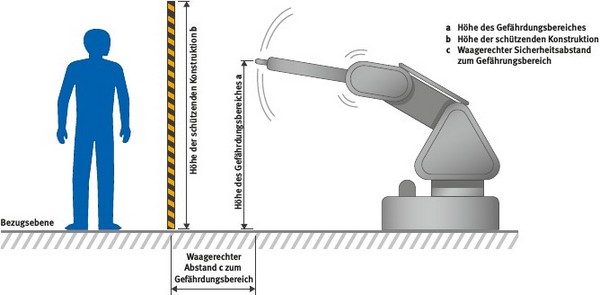
Abb. 79
Robotersystem mit gesichertem Gefahrenbereich. Die exakten Maße sind den Tabellen 4 und 5 der EN ISO 13857 zu entnehmen.
Dabei muss darauf geachtet werden, dass das sicherheitstechnische Niveau der erforderlichen Schutzmaßnahmen (u. a. Schutzeinrichtungen, Sicherheitskreise) bzgl. der einzelnen Gefahrenbereiche gegeben ist. Zusätzlich ist darauf zu achten, dass das sicherheitstechnische Niveau der Spritzgießmaschine nicht verringert wird.
Sichern Sie die Gefahrbereiche der Industrieroboter, Handlingsysteme, Angusspicker etc. gegen Zugriff bzw. gegen unbefugtes Betreten. In der Regel werden Zäune, Verdeckungen etc. eingesetzt. Die Zäune dürfen nicht übersteigbar oder unterschreitbar sein.
Bei Fehlverfahren der Rotoberanlage muss die bedienende Person durch mechanische Anschläge (Puffer), durch eine sicher überwachte Industrierobotersteuerung oder durch eine ausreichende Festigkeit der Umzäunung geschützt werden.
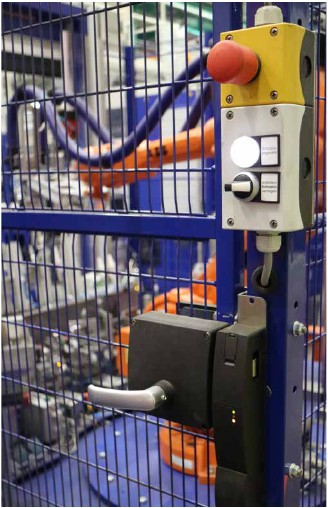
Abb. 80
Sicherung von Zugangstüren
Sichern Sie Zugänge zu den Anlagen durch Positionsschalter ab. Beim Öffnen der Tür darf keine gefahrbringende Bewegung mehr stattfinden. Das alleinige Schließen der Tür darf nicht zum Wiederanfahren der Anlage führen.
Es hat sich bewährt, an Zugangstüren Positionsschalter mit Zuhaltung vorzusehen.
Der Zugang zum Industrieroboterbereich kann auch durch Lichtschranken, Laserscanner und anderen berührungslos wirkenden Schutzeinrichtungen gesichert sein.
Setzen Sie für das Einrichten von Industrieroboteranlagen und zur Störungsbeseitigung ausreichend qualifiziertes Personal ein.
Rüsten Sie die Industrieroboteranlagen mit einem Not-Halt aus. Dieser muss mit der Steuerung der Spritzgießmaschine verknüpft sein.
Nach Entriegelung der Not-Halt-Einrichtung darf weder die Industrieroboteranlage noch die Spritzgießmaschine direkt wieder anlaufen. Dieses muss über einen zusätzlichen Startbefehl erfolgen.
Zur Programmierung/Justierung des Industrieroboters kann ein Einzelbetrieb vorgesehen werden, wenn der Schutz der Bedienerin bzw. des Bedieners gewährleistet ist.
Beim Einsatz von kollaborierenden Industrierobotern sind durch das Zusammenwirken von Mensch und Maschine besondere Sicherungsmaßnahmen zu beachten. Weitere Informationen dazu finden Sie in Kapitel 5 der DGUV Information 209-074 "Industrieroboter".
3.3.9
Arbeiten im Hochregallager
Beim Spritzgießen werden leichte und großvolumige Formteile in großen Stückzahlen produziert. Zur Lagerung werden sowohl automatisierte als auch manuell betriebene Läger genutzt. Hierbei kommen z. B. Regalbediengeräte (automatisierte Läger) oder Regalflurförderzeuge (Schmalgangläger) zum Einsatz. Bei Störungen etc. in den Regalen wird eine Arbeit in großer Höhe erforderlich, was erhebliche Absturzgefahren birgt. Weiterhin kann es zu Gefährdungen im Rahmen der Kommissionierarbeiten kommen.
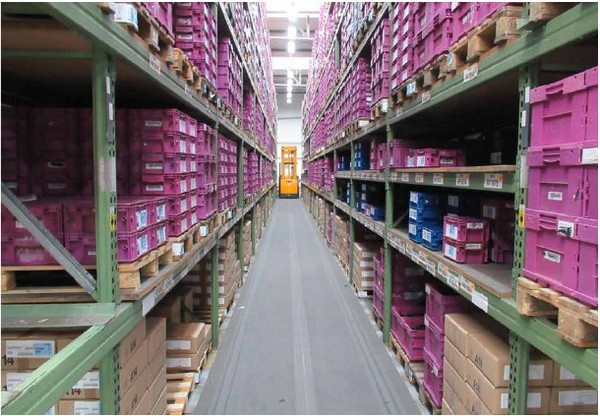
Abb. 81
Schmalganglager
![]() | Rechtliche Grundlagen |
---|---|
|
![]() | Weitere Informationen |
---|---|
|
![]() | Gefährdungen |
---|
Schmalgangläger und automatisierte Läger zeichnen sich durch große Lagerkapazität bei geringem Platzbedarf aus. Sie werden daher auch zunehmend in Spritzgießbetrieben verwendet. Bei der Ein- und Auslagerung von Rohstoffen und Fertigwaren, dem Bedienen von Regalbediengeräten und Regalflurförderzeugen, bei der Störungsbeseitigung und beim Retten von Personen kann es u. a. zu folgenden Gefährdungen kommen:
Paletten können aufgrund von Verschiebung ihrer Ladung oft nicht mehr von den Regalbediengeräten aufgenommen werden. Verhaken sich Paletten mit Regalteilen, kann zusätzlich die Gefahr des Absturzes der Ware bestehen. Zur Beseitigung der Störungen muss unter Umständen in das Regal eingestiegen oder das Lastaufnahmemittel des Regalbediengerätes betreten werden. Hierbei besteht Absturzgefahr.
Die Störung kann oftmals von dem Lastaufnahmemittel des Regalbediengerätes aus beseitigt werden. Hier besteht ebenfalls Absturzgefahr, wenn sich die Bedienerin bzw. der Bediener aus dem Regalbediengerät herauslehnt.
Bei der Störungsbeseitigung kann es vorkommen, dass vom Lastaufnahmemittel aus ins Regal eingestiegen werden muss. Auch hier besteht Absturzgefahr.
Bei Störung des Regalbediengerätes besteht die Gefahr, dass die Bedienenden den Bedienstand aufgrund der Höhe nicht gefahrlos verlassen können.
Wenn eine Person infolge eines Absturzes in einem Auffanggurt hängt, besteht die Gefahr, dass die die Blutzirkulation stark beeinträchtigt wird. Die Folge können Bewusstlosigkeit oder der Tod sein.
Hochregallager sind oftmals als Schmalgassenlager ausgeführt. Bei Schmalganglägern besteht die Gefahr, dass aufgrund fehlender Sicherheitsabstände Fußgängerinnen und Fußgänger von den Regalflurförderzeugen erfasst werden können.
Sowohl bei Schmalganglägern als auch bei automatisierten Lägern besteht Gefahr für Fußgängerinnen und Fußgänger. Das gilt insbesondere bei manuellen Kommissionierarbeiten, Störungsbeseitigungen etc.
![]() | Maßnahmen |
---|
Die Sicherungsmaßnahmen bei Arbeiten in Hochregallagern, insbesondere der Störungsbeseitigung, sind stark vom Ort und Art der Störung abhängig. Die im Folgenden aufgelisteten Maßnahmen geben lediglich einen Überblick über mögliche Sicherungsmaßnahmen. Detaillierte Maßnahmen können Sie der DGUV Information 208-045 "Fördertechnik in Hochregallägern - Störungsbeseitigung in Regalanlagen" entnehmen.
Sorgen Sie dafür, dass vor dem Betreten des Schmalgassenlagers bzw. vor Einstieg in die Gasse das Regalbediengerät abgeschaltet oder auf Handbetrieb umgeschaltet und gegen Wiedereinschalten gesichert wird (Lockout/Tagout "LOTO", siehe Abschnitt 3.2.1)
Bei Arbeiten im Regal oder auf dem Lastaufnahmemittel müssen Beschäftigte gegen Absturz gesichert sein.
Sichern Sie begehbare Lastaufnahmemittel zur Regalgasse hin mit einem Geländer gegen Absturz.
Bringen Sie zur Befestigung persönlicher Schutzausrüstungen gegen Absturz eine tragfähige und stabile Anschlagmöglichkeit an den Regalen selbst oder am Gebäude an.
Sorgen Sie dafür, dass Nebenarbeiten in Schmalgängen nur durchgeführt werden, wenn diese Gänge gegen das Einfahren von Regalförderzeugen gesperrt sind und die hierzu verwendete Einrichtung gegen unbefugtes oder irrtümliches Entfernen gesichert wurde.
Beim Einstieg in das Regal kann eine Aluminiumschiene, ein Einlegeboden oder eine benachbarte Leerpalette als sichere Standfläche dienen. Treffen Sie zusätzlich Maßnahmen gegen Absturz, z. B. Bereitstellung von persönlichen Schutzausrüstungen gegen Absturz.
Sorgen Sie dafür, dass Personen im Falle eines Absturzes unverzüglich gerettet und ärztlich versorgt werden. Dieses kann durch den Einsatz von Personen-Notsignal-Anlagen oder einem Sicherungsposten gewährleistet werden.
Unterweisen Sie die Beschäftigten mindestens einmal jährlich über den Gebrauch der persönlichen Schutzausrüstungen und deren ordnungsgemäße Aufbewahrung sowie das Erkennen von Schäden an der Schutzausrüstung. Dieses beinhaltet auch eine praktische Übung.
Stellen Sie sicher, dass nur Personen, die dazu gesundheitlich in der Lage sind, Arbeiten in der Höhe durchführen.
Sorgen Sie dafür, dass in Ihrem Regallager Personen in der Rettung von Menschen, die in den Gurt gestürzt sind, ausgebildet werden. Es ist von großer Bedeutung, dass Verunfallte kompetent und schnell aus der hängenden Position gerettet werden können. Auch dies sollte mindestens einmal im Jahr geübt werden.
In Schmalganglagern muss ein Schutzkonzept für Fußgängerinnen und Fußgänger erstellt werden, das z. B. stationäre Warnanlagen oder Personenerkennungssysteme vorsieht.
3.3.10
Betreiben von Separierern
Separierer werden in Spritzgießbetrieben häufig zum automatischen Trennen von unterschiedlich großen Formteilen oder zum Trennen von Formteilen und Angüssen eingesetzt. Durch die Drehbewegung der Separierer besteht die Gefahr, dass es zu Quetschungen der Finger oder Hand kommt. Ebenso kann Kleidung gefangen und eingezogen werden.
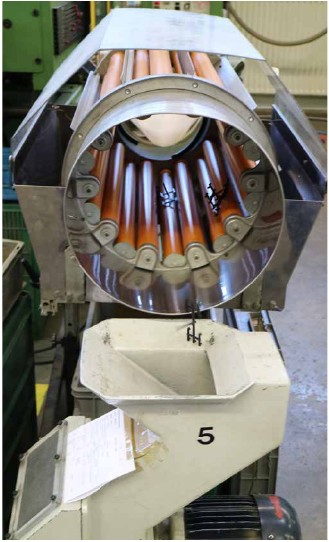
Abb. 82
Trommelseparierer

Abb. 83
Schneckenseparierer
![]() | Gefährdungen |
---|
Zum Trennen von Angüssen und fertigen Formteilen werden in Spritzgießbetrieben Separierer eingesetzt.
Diese werden in der Regel als Beistellgeräte betrieben und sind nicht mit der Spritzgießmaschine oder weiteren Handlinggeräten verkettet.
Beim Betreiben von Separieren kann es u. a. zu folgenden Gefährdungen kommen:
Durch das Hineingreifen in Trommelseparierer können die Finger oder die Hand gequetscht werden.
Beim Eingriff in die laufende Walze des Schneckenseparierers besteht ebenfalls eine Quetsch- und Schergefahr.
Lange Haare sind besonders gefährdet, an den drehenden Teilen der Separierer eingezogen zu werden. Dies gilt auch für Ketten, Ringe, Uhren und anderen Schmuck.
Bei Arbeiten an oder in der Nähe von Trommel- bzw. Schneckenseparierern können Handschuhe und Kleidungstücke gefangen oder eingezogen werden, wodurch auch Gliedmaßen geschädigt werden können.
Separierer werden oftmals nicht in die Steuerung der Spritzgießmaschinen integriert, sondern als separate Maschine betrieben. Gleichwohl werden sie meist durch Förderbänder beschickt, sodass es eine indirekte Verbindung zur Spritzgießmaschine gibt. Anhand dieser verketteten Anlagen kann es zu neuen Gefährdungen durch Einzugs- und Fangstellen kommen.
Da Separierer meist als "Beistellgeräte" genutzt werden, ragen diese oftmals in Verkehrswege und gefährden Fahrer und Fahrerinnen von Gabelstaplern sowie Fußgängerinnen und Fußgänger.
Durch Separierer kann der Arbeitsraum von den Bedienenden eingeschränkt werden.
Separierer werden oft an verschiedenen Stellen im Betrieb eingesetzt. Bei Nichtgebrauch werden sie ebenfalls räumlich verändert. Durch die ständigen Bewegungen können Beschädigungen an den stromführenden Teilen entstehen. Dies kann zu einem lebensbedrohlichen Stromschlag führen.
![]() | Maßnahmen |
---|
Die Vermeidung von Unfällen an Separieren können Sie u. a. durch folgende Maßnahmen realisieren:
Vermeiden Sie Angüsse durch den Einsatz von Heißkanalwerkzeugen. Dies wirkt sich auf Dauer auch wirtschaftlich positiv aus.
Sichern Sie Fang-, Quetsch-, Einzugs- und Scherstellen gegen Berühren oder Hineingreifen.
Verwenden Sie Separierer mit Zugkraftüberwachung. Dies verhindert Unfälle und schützt die Formteile vor Beschädigung.
Entfernen Sie verhakte Formteile nur bei ausgeschaltem Separierer. Unterweisen Sie Ihre Beschäftigten entsprechend.
Weisen Sie an, dass in der Nähe von Separierern nur enganliegende Kleidung getragen wird. Lange Haare sind mit einem Haarnetz zu schützen. Verbieten Sie das Tragen von Schmuck wie Uhren, Ringe und Ketten.
Bei Arbeiten in der Nähe von Separierern dürfen keine Handschuhe getragen werden.
Berücksichtigen Sie den Platzbedarf der Separierer bereits bei der Planung. So vermeiden Sie, dass diese in Verkehrswege ragen oder den Arbeitsplatz des Bedienenden einengen.
Weisen Sie an, dass bei jeder Wiederinbetriebnahme eine Sichtkontrolle des Separierers durchgeführt wird. Bei augenscheinlichen Schäden darf das Gerät nicht in Betrieb genommen werden.
3.3.11
Betrieb von Vertikal-Spritzgießmaschinen
Vertikal-Spritzgießmaschinen werden insbesondere bei der Produktion von Formteilen mit Einlegeteilen betrieben. Die Gefährdungen an diesen Maschinen gehen über die der Horizontalmaschinen hinaus. Dies gilt beispielsweise für Gefährdungen beim Einrichten sowie beim manuellen Hantieren in dem geöffneten Spritzgießwerkzeug, wobei es zu Schnittverletzungen kommen kann.
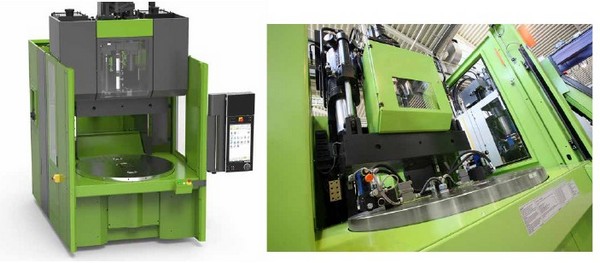
Abb. 84 a + b
Vertikal-Spritzgießmaschinen
![]() | Gefährdungen |
---|
Beim Betreiben von Vertikal-Spritzgießmaschinen ergeben sich im Wesentlichen die gleichen Gefährdungen wie bei den Horizontal-Spritzgießmaschinen.
Darüber hinaus können insbesondere noch folgende Gefährdungen auftreten:
Bei manuellen Tätigkeiten im Werkzeugbereich kann in bewegte Maschinen- und Werkzeugteile eingegriffen werden, wodurch sich Quetschgefahren ergeben.
Am Öffnungs- und Schließmechanismus der Spritzgießmaschine bestehen weitere Quetschgefahren.
Bei der Verwendung von Zweihand-Steuerungen besteht die Gefahr, dass eine zweite Person in den Gefahrbereich der Maschine eingreift.
An älteren Spritzgießmaschinen wurden Fußschalter als Befehlseinrichtung verbaut, die nicht mehr dem Stand der Technik entsprechen und ggf. einen Eingriff in ungesicherte Gefahrstellen ermöglichen.
Beim nicht bestimmungsgemäßen Einsatz von zu großen Werkzeugen kann der erforderliche Sicherheitsabstand von Lichtgittern bzw. - vorhängen zur Gefahrstelle unterschritten werden.
Die Materialzufuhr ist bauartbedingt meist hoch gelegen. Beim Befüllen, Reinigen etc. besteht Absturzgefahr.
Beim manuellen Einlegen von Rohlingen bzw. Entnehmen von Formteilen besteht die Gefahr von Schnittverletzungen an Auswerfern und Trennkanten.
Wenn Kabel, Schläuche, Stangen und dergleichen angespritzt werden und aus der festen Schutzeinrichtung herausragen, besteht die Möglichkeit, durch die Öffnungen in den Gefahrbereich von Spritzgießwerkzeug, Auswerfern etc. einzugreifen.
Bei Tätigkeiten am Spritzgießwerkzeug besteht die Gefahr, sich an dem heißen Werkzeug, dem Heißkanal oder anderen heißen Gegenständen zu verbrennen, wenn manuelle Einlegearbeiten durchgeführt werden.
Aus dem Heißkanal kann flüssige Schmelze austreten, welche die Maschinenbedienenden bzw. -einrichtenden an Händen, Armen oder im Gesicht treffen kann.
Beim Einrichten der Spritzgießmaschine besteht die Gefahr, dass das Spritzgießwerkzeug oder Teile davon nach unten fallen und Handverletzungen verursachen.
Beim Anspritzen von langen Einlegeteilen besteht die Gefahr, dass diese in den Arbeits- bzw. Verkehrsbereich hineinragen und zur Stolpergefahr werden.
![]() | Maßnahmen |
---|
Stellen Sie sicher, dass die Instandhaltungsarbeiten nur bei einer sicher blockierten Aufspannplatte erfolgen.
Stellen Sie sicher, dass beim manuellen Einlegen in die Spritzgießmaschine oder in die Peripherieeinheit kein Eingriff in bewegte Maschinen- und Werkzeugteile möglich ist. Dazu haben sich bewegliche, trennende Schutzeinrichtungen wie verriegelte Tunnelhauben bewährt.
Diese Schutzeinrichtungen müssen auch wirksam sein, wenn lange Gegenstände wie Kabel oder Stangen eingelegt werden. Dies bedeutet, dass die vorgesehenen Öffnungen so ausgelegt sein müssen, dass im Gefahrenbereich auch bei nicht eingelegtem Teil keine Gefahrstellen erreicht werden können.
Dies gilt auch für die Gefahrstellen im Bereich des Öffnungs- und Schließmechanismus der Spritzgießmaschine.
Fußschalter sind als Befehlseinrichtung nicht zulässig. Hier ist eine Nachrüstung auf den Stand der Technik erforderlich.
Zweihand-Schaltungen sind nur zulässig, wenn andere Schutzeinrichtungen nicht möglich sind.
Es muss durch weitere feste Schutzeinrichtungen gewährleistet sein, dass der Eingriff einer zweiten Person in den Gefahrbereich der Maschine ausgeschlossen ist.
Stellen Sie sicher, dass ggf. der erforderliche Sicherheitsabstand von Lichtgittern bzw. -vorhängen vorhanden ist.
Achten Sie auf die Angaben des Herstellers zur maximal zulässigen Werkzeuggröße.
Sorgen Sie dafür, dass hoch gelegene Arbeitsbereiche wie Materialtrichter möglichst automatisch befüllt werden. Da diese Bereiche generell erreicht werden müssen, lassen Sie feste Aufstiegshilfen, Podeste etc. installieren.
Durch die Installation von festen Aufstiegshilfen, Podesten etc. kann es möglich sein, dass Gefahrstellen von dieser Position aus erreicht werden können. Stellen Sie sicher, dass von diesen Bereichen aus keine Gefahrbereiche im Werkzeug- oder Peripheriebereich erreicht werden können.
Weisen Sie an, dass bei manuellen Arbeiten am Spritzgießwerkzeug Schnittschutzhandschuhe und ggf. schnittfester Unterarmschutz getragen werden.
Dies reicht meist auch aus, um vor Verbrennungen an heißen Spritzgießwerkzeugteilen zu schützen.
Lochbleche sind in Tunnelhauben unzulässig, es müssen z. B. Verdeckungen aus Acrylglas oder Polycarbonat vorgesehen werden.
Beim Einrichten bzw. beim Materialwechsel ist zusätzlich ein Visier zu tragen, um vor eventuell herausspritzender Schmelze geschützt zu sein.
Stellen Sie sicher, dass das Werkzeugoberteil bzw. Teile davon nicht nach unten fallen können. Dies kann z. B. durch eine formschlüssige Sicherung erfolgen.
Sehen Sie ausreichend Arbeits- und Verkehrsbereiche an der Spritzgießmaschine vor.
3.3.12
Verarbeitung von Duroplasten
Die Herstellung von Formteilen aus duroplastischen Kunststoffen erfolgt vielfach auch mit Spitzgießmaschinen. Im Wesentlichen sind die Gefährdungen mit denen der Thermoplast-Verarbeitung vergleichbar. Das Unfallgeschehen zeigt jedoch, dass es beim Duroplast-Spritzgießen einige besondere Schwerpunkte gibt, die individuelle Maßnahmen erforderlich machen.
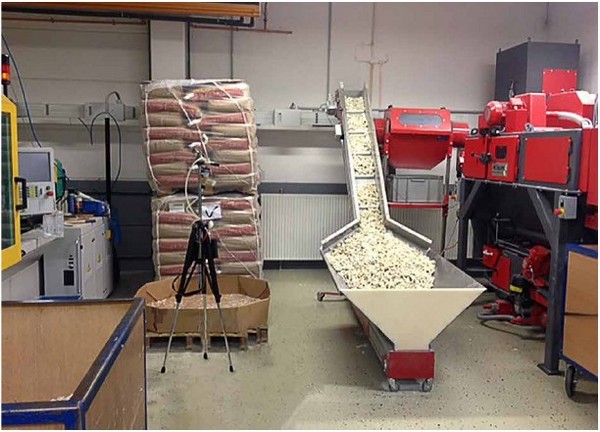
Abb. 85
Materialversorgung und automatische Formteilentgratung bei Duroplast-Spritzgießmaschinen
![]() | Gefährdungen |
---|
Bei der Verarbeitung von Duroplasten auf Spritzgießmaschinen gelten weitgehend dieselben Rahmenbedingungen wie beim Spritzgießen von Thermoplasten. Daher gelten die bereits in der Branchenregel aufgeführten Gefährdungen und Maßnahmen auch in dieser Art der Fertigung. Einer der wesentlichen Unterschiede bei der Verarbeitung ist, dass Duroplaste meist mit einer recht niedrigen Temperatur in das Werkzeug eingespritzt werden und dort unter Zufuhr einer hohen Temperatur von bis zu 250 °C aushärten. Das fertige Formteil wird in aller Regel im heißen Zustand entformt.
Durch die Verarbeitung von Duroplasten können sich darüber hinaus folgende spezifische Gefährdungen ergeben:
Durch hohe Verarbeitungstemperaturen erhöht sich insbesondere die Gefahr von Verbrennungen an Spritzgießwerkzeugen und an den fertigen Formteilen. Auch an der Plastifiziereinheit besteht Verbrennungsgefahr.
Oftmals kommt es zu "Überspritzungen", die nach dem Entformen abplatzen. Durch diese kann es auf den Böden zu Rutschgefahren kommen. Das gilt auch für Stäube und Granulate, die durch die Rohstoff-Zufuhr frei werden können.
Duroplast-Formteile sind meist sehr hart und scharfkantig, was zu Schnittverletzungen beim manuellen Hantieren mit den Formteilen führen kann. Dies gilt beispielsweise beim Aussortieren von Angüssen, Fehlteilen und dergleichen.
Beim Einspritzen der nur etwa 30 bis 110 °C warmen Schmelze kommt es aufgrund der Füllstoffe zu einem schlechten Fließverhalten. Dies führt des Öfteren zu Verstopfungen im Bereich der Düse oder des Kaltkanals. Bei der notwendigen Störungsbeseitigung kommt es zu Gefährdungen der Hände durch scharfkantige Auswerfer, Trennkanten, Handwerkzeugen etc.
Aufgrund des schmalen Temperaturbereichs für die Verarbeitung der Duroplaste besteht eine erhöhte Gefahr der Überhitzung, sodass Gefahrstoffe wie Phenol oder andere Zersetzungsprodukte (siehe Abschnitt 3.1.9) entstehen können.
Die zu verarbeitenden Duroplaste können als Granulate oder in pulverförmigem Zustand vorliegen. In beiden Fällen kann es zu einer Freisetzung von Stäuben kommen.
Auch bei der Nachbearbeitung der Formteile, hier insbesondere beim maschinellen Entgraten, können Stäube entstehen.
Beim Umfüllen von Duroplast-Formteilen entsteht Lärm in einer Höhe, die über den Auslöseschwellen liegen kann.
![]() | Maßnahmen |
---|
Sorgen Sie dafür, dass die Hallenböden frei von Verunreinigungen gehalten werden. In der Regel sind mehrere Reinigungsvorgänge pro Schicht erforderlich, um die Böden rutschfrei zu halten.
Veranlassen Sie, dass Schutzhandschuhe und ggf. schnittfester Unterarmschutz getragen werden. Dies gilt insbesondere bei Tätigkeiten im Bereich des Spritzgießwerkzeugs und bei der manuellen Nachbearbeitung der Formteile.
Die Schutzhandschuhe reichen meist auch aus, um Verbrennungen an den noch heißen Formteilen zu vermeiden.
Ermitteln Sie die Exposition der Beschäftigten gegenüber Gefahrstoffen bei der Verarbeitung in der Spritzgießmaschine. Sehen Sie ggf. Absaugungen über Schnecke bzw. Werkzeug vor.
Ermitteln Sie die Exposition der Beschäftigten gegenüber Stäuben. Sehen Sie ggf. Absaugungen beim Ein- und Umfüllen des Rohstoffs vor. Auch im Einfüll- und Austragsbereich von Entgratungsautomaten können Absaugungen erforderlich sein.
Ermitteln Sie die Höhe der Lärmexposition der Beschäftigten. Hier sind insbesondere Bereiche an den Spritzgießmaschinen, an Entgratungsautomaten sowie bei Umfüllvorgängen und Reinigungstätigkeiten zu betrachten. Stellen Sie ggf. Gehörschutz zur Verfügung, wenn technische Lärmminderung nicht möglich ist.
Beste Praxis
Das Tragen von Schutzhandschuhen am Sortiertisch vermeidet Schnittverletzungen an den Händen.
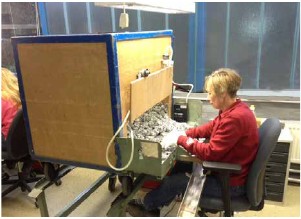
Abb. 86
Sortierarbeitsplatz
3.3.13
Spezielle Spritzgieß-Verfahren
Im Bereich des Spritzgießens gibt es eine große Anzahl von Spezialanwendungen, wie das Mehrkomponenten-, Innendruck-, Schaumstoff-, In-Mould- oder Extrusionsspritzgießen. Auch die Verwendung von Tandem-Werkzeugen ist üblich. Die sich hier zusätzlich ergebenden Gefährdungen machen individuelle Schutzmaßnahmen erforderlich.
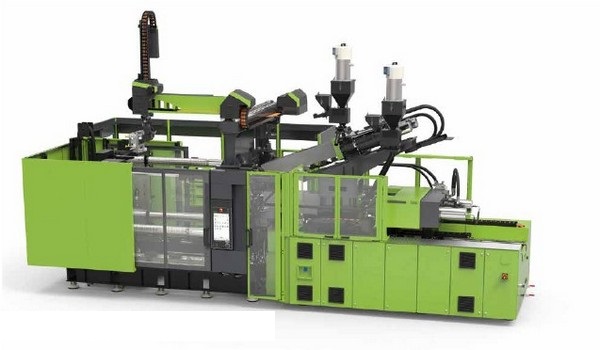
Abb. 87
Mehrkomponentenspritzgießmaschine
![]() | Gefährdungen |
---|
Bei Spezialanwendungen des Spritzgießens kommt es zu den Gefährdungen, die bereits in dieser Branchenregel behandelt wurden. Es kann darüber hinaus zu spezifischen Gefährdungen kommen, wobei im Folgenden nur die wesentlichen Themen betrachtet werden.
Mehrkomponenten-Spritzgießmaschinen
Hier werden unterschiedliche Komponenten (Kunststofftypen, Kunststofffarben) in verschiedenen Plastifiziereinheiten geschmolzen und nacheinander in ein Spritzgießwerkzeug eingespritzt. Das Werkzeug wird verschoben, gedreht, oder arbeitet mit der Kern-Rückzugstechnik.
Dabei können sich folgende Gefährdungen ergeben:
Bauartbedingt gibt es durch das Mehr an Plastifiziereinheiten hochgelegene Arbeitsbereiche, an denen Absturzgefahr besteht.
Es gibt deutlich mehr heiße Maschinenteile, an denen Verbrennungsgefahr besteht.
Die Störanfälligkeit ist oftmals höher. Aus diesem Grunde muss häufiger in den Werkzeugbereich der Spritzgießmaschine eingegriffen werden. Dadurch ergeben sich zusätzliche Schnitt- und Verbrennungsgefahren.
Gas-Innendruck-Verfahren und Fluidinjektionstechnik
Bei diesen Technologien werden die Formteile temporär mit einem Füllstoff wie Gas oder Wasser versehen, um hohle Werkstücke zu produzieren. Dabei kommt es zu folgenden, zusätzlichen Gefährdungen:
Bei der Druckentlastung des Formteils kann gehörschädigender Lärm entstehen.
Durch den Schallpegel der Druckentlastung können sich Beschäftigte erschrecken, was zu Unfällen führen kann.
Schaumstoff-Spritzgießen
Gängig ist das chemische Schäumen, wobei dem Granulat ein Treibmittel zugeführt wird, das im Spritzgießwerkzeug dafür sorgt, dass das Formteil aufschäumt. Dabei kann es zu folgenden, zusätzlichen Gefährdungen kommen:
Durch den verwendeten Kunststoff wie beispielsweise Polystyrol sowie durch das Treibmittel kann es zu einer Exposition gegenüber Gefahrstoffen kommen.
Die verwendeten Granulate und Treibmittel sind oftmals leicht entzündlich, sodass eine Brand- und Explosionsgefahr besteht.
In-Mould-Spritzgießen
Beim In-Mould-Verfahren werden im Spritzgießwerkzeug eingelegte Materialien hinterspritzt. Dies können z. B. Beschriftungsfolien oder Hartschaum sein. Als zusätzliche Gefährdungen können auftreten:
Eine erhöhte Störungsanfälligkeit der Produktion erfordert mehr manuelle Eingriffe in das Spritzgießwerkzeug sowie in die Peripherieanlagen. Dies birgt die Gefahr von Quetsch- und Schnittverletzungen.
Oftmals werden großvolumige Formteile wie Eimer hergestellt, in Peripherieanlagen gestapelt und ausgeschleust. Dabei ist unter Umständen ein Eingriff in bewegte Maschinenteile möglich.
Extrusionsspritzgießen
Beim Extrusionsspritzgießen werden z. B. lange, dünnwandige und strukturierte Formteile gefertigt oder Rohlinge gespritzt, die in der Folge zu Hohlkörpern wie PET-Flaschen geblasen werden. Es handelt sich in der Regel um verkettete Anlagen.
Eine erhöhte Störungsanfälligkeit der Produktion erfordert mehr manuelle Eingriffe in das Spritzgießwerkzeug sowie in die Peripherieanlagen. Dies birgt die Gefahr von Quetsch- und Schnittverletzungen.
Verwendung von Tandem-Werkzeugen
Bei Tandem-Werkzeugen gibt es zwei Trennebenen, die die Abkühlung eines Formteils ermöglichen, während die zweite Kavität gefüllt wird.
In den Tandem-Werkzeugen gibt es deutlich mehr Quetsch- und Scherstellen als in einem Standard-Werkzeug.
Durch die komplexere Steuerung gibt es eine höhere Anfälligkeit für Störungen.
![]() | Maßnahmen |
---|
Mehrkomponenten-Spritzgießmaschinen
Sorgen Sie dafür, dass feste Aufstiegshilfen wie Treppen oder Podeste für die höher gelegenen Arbeitsplätze vorhanden sind.
Lassen Sie heiße Maschinenteilen isolieren und stellen Sie ggf. Thermohandschuhe zur Verfügung.
Optimieren Sie die Betriebsabläufe so, dass ein störungsfreier Betrieb, bei dem Eingriffe in Maschinen und Spritzgießwerkzeuge weitgehend vermieden werden, möglich ist.
Gas-Innendruck-Verfahren und Fluidinjektionstechnik
Sorgen Sie für eine effiziente Lärmminderung bei der Druckentlastung. Dies kann z. B. mit Schalldämpfern oder Lärmkapselungen erfolgen.
Schaumstoff-Spritzgießen
Ermitteln Sie Exposition der Beschäftigten gegenüber Gefahrstoffen und Stäuben, ggf. sind Absaugungen erforderlich.
Der Einsatz automatischer Branderkennungs- und Löschsysteme hat sich bewährt. Zu Explosionsschutzmaßen siehe Abschnitt 3.1.10.
In-Mould-Spritzgießen, Extrusionsspritzgießen, Verwendung von Tandem-Werkzeugen
Sorgen Sie für einen störungsfreien Betrieb, bei dem Eingriffe in Maschinen und Spritzgießwerkzeuge weitgehend vermieden werden.
Notizen
_______________________________________________________________________________
_______________________________________________________________________________
_______________________________________________________________________________
_______________________________________________________________________________
_______________________________________________________________________________
_______________________________________________________________________________
_______________________________________________________________________________
_______________________________________________________________________________
_______________________________________________________________________________
_______________________________________________________________________________
_______________________________________________________________________________
_______________________________________________________________________________
_______________________________________________________________________________
_______________________________________________________________________________
_______________________________________________________________________________
_______________________________________________________________________________
_______________________________________________________________________________
_______________________________________________________________________________
_______________________________________________________________________________
_______________________________________________________________________________
_______________________________________________________________________________
_______________________________________________________________________________
_______________________________________________________________________________
_______________________________________________________________________________
_______________________________________________________________________________
_______________________________________________________________________________
_______________________________________________________________________________
_______________________________________________________________________________
_______________________________________________________________________________
_______________________________________________________________________________
_______________________________________________________________________________
_______________________________________________________________________________
_______________________________________________________________________________
_______________________________________________________________________________
_______________________________________________________________________________
_______________________________________________________________________________
Deutsche Gesetzliche
Unfallversicherung e.V. (DGUV)
Glinkastraße 40
10117 Berlin
Telefon: 030 13001-0 (Zentrale)
E-Mail: info@dguv.de
Internet: www.dguv.de
Tragepflicht ab 85 dB(A)